This blog outlines the key aspects of Simplified Emergency Maintenance Process in S4 HANA Asset Management (Cloud & On-Premise). When a technical object has a malfunction, we must plan the required repair work, as well as document and confirm the maintenance work with root cause when it is done. SAP has introduced “Report and Repair Malfunction” functionality to support maintenance technician to process malfunction activities for effective management of malfunctions.
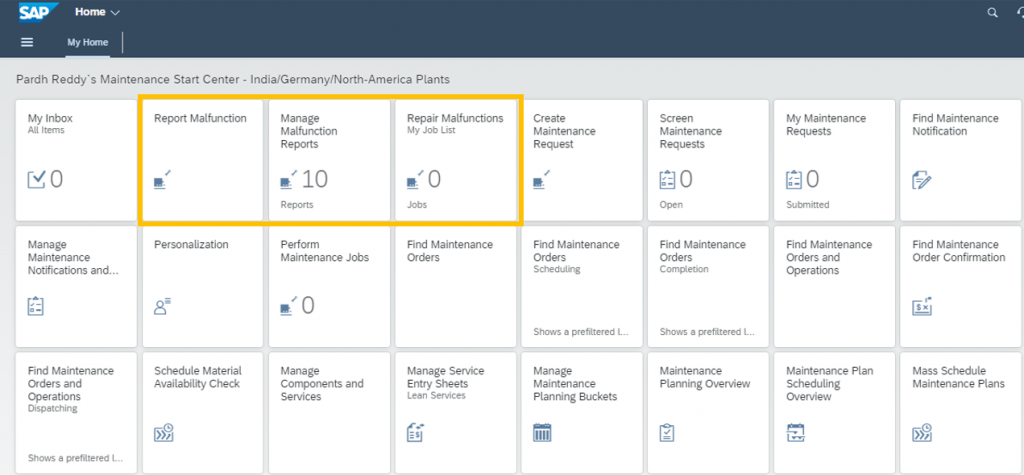
Fact Sheet: The Breakdown Maintenance can be performed using various standard processes, Viz:
- Corrective Maintenance (Standard Process) – Merge steps Create/Plan/Release into a single step.
- Reactive Maintenance (Using Phase Model) with scope ID 4HH in SAP Best Practices, where system skips Screening/Planning/Approval – App ID F1511A
- Emergency Maintenance, where all the steps are covered in one Fiori App ID F2023 – Scope ID BH2 in SAP Best Practices is using this app.
Moving ahead, I will walk you through the “Report and Repair Malfunction” using Fiori App ID F2023.
Three tiles are provided with App ID F2023, i.e.
- Report Malfunction Tile – Is used to create malfunction reports
- Manage Malfunction Reports Tile – Is used to have the list of malfunction reports that have already been created
- Repair Malfunctions-My Job List Tile – Is used to have the list of work items which were assigned to Me and My Team.
My Business Use Case:
One of the cooling water circulation pumps in KILN area has got malfunction, where the Tyre Coupling of the pump damaged. For instance, I wear “Lead Maintenance Technician” hat and perform all the necessary steps that are required to capture the malfunction…let`s dive in…
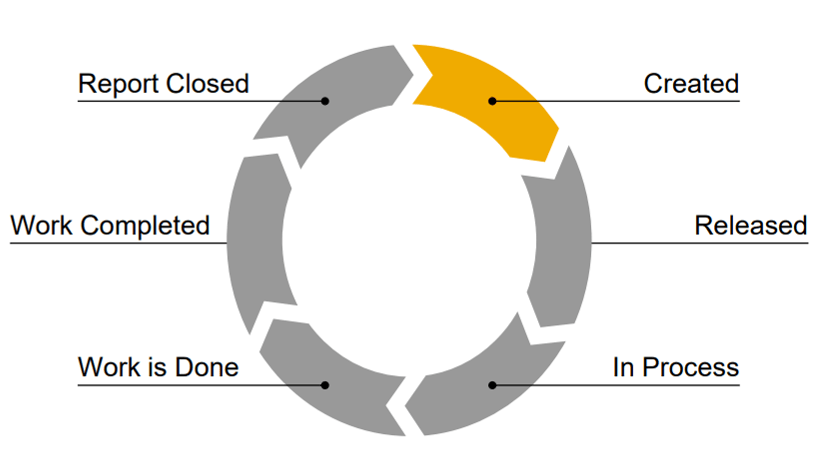
One must have completed below tasks to leverage “Report Malfunction” functionality using Fiori App ID F2023
- Synchronize business partners with employee code so that the lead technician can assign work items to different maintenance technicians and choose respective employee numbers from value help.
Employee Master:

Business Partner and Employee master synchronization:
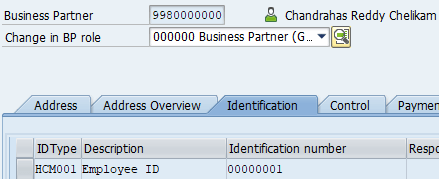
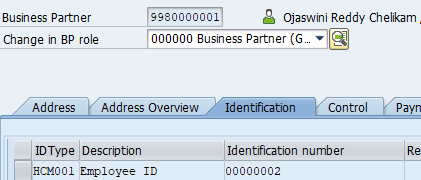
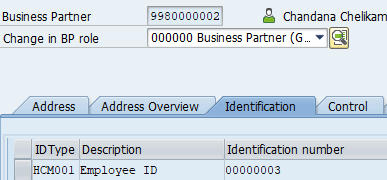
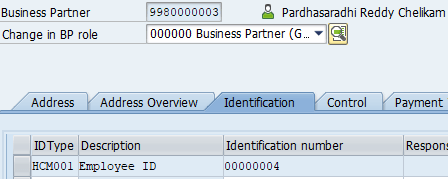
Then assign the employee code to respective work center, so that each employee spent hours cost can be tracked in the workorder.
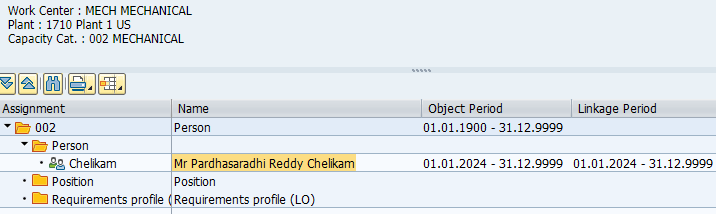
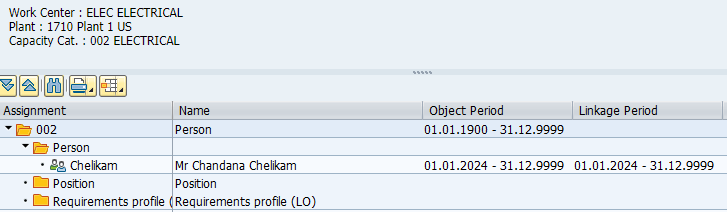
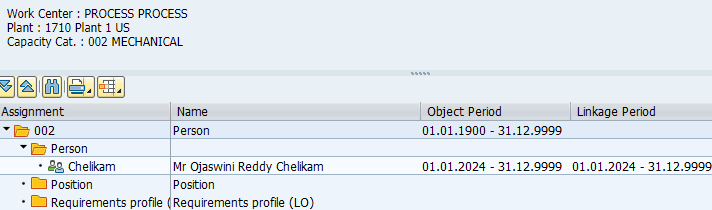
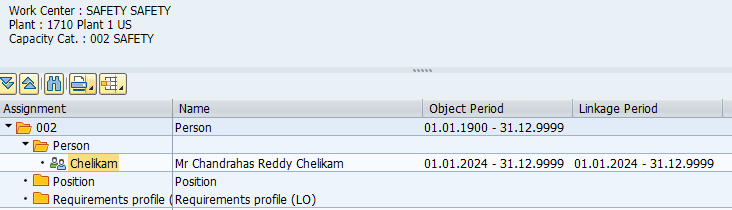
- Overall status profile “MAINTJOB” for malfunction report

Events of Status Profile: These events are meant for updating malfunction work item status for each user action
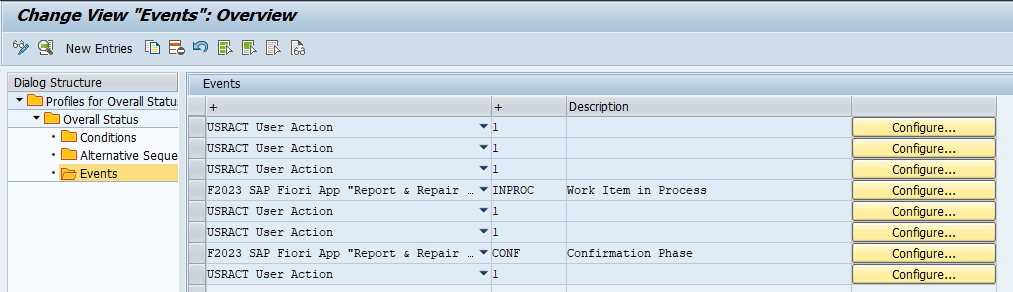
for example:
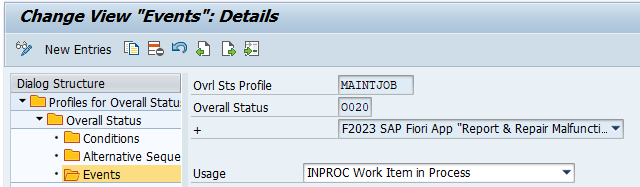
- Assignment of overall status profile “MAINTJOB” to Notification Type:
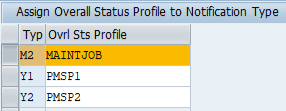
- Assignment of overall status profile “MAINTJOB” to Order Type:
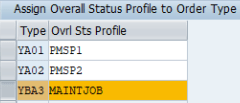
- Assignment of Notification Type to Malfunction Report origin against respective Planning Plant:
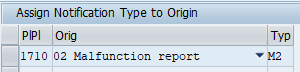
- Assignment of Notification Type to Order Type:
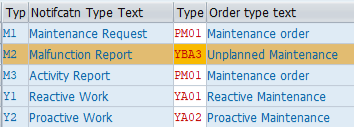
Now, let us get into transaction details of “Report and Repair Malfunction”,
Report Malfunction: Create a malfunction report with all the relevant information required.
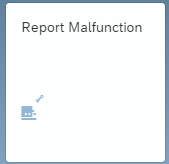
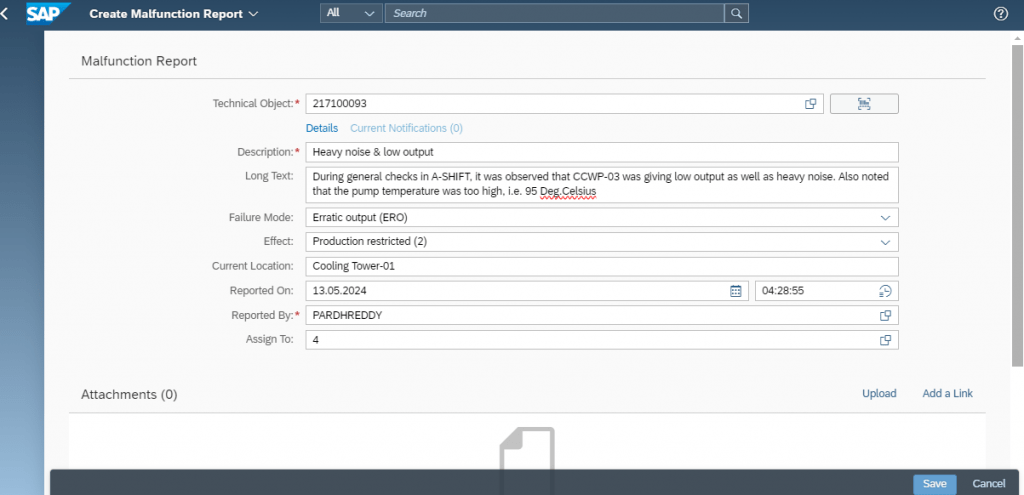
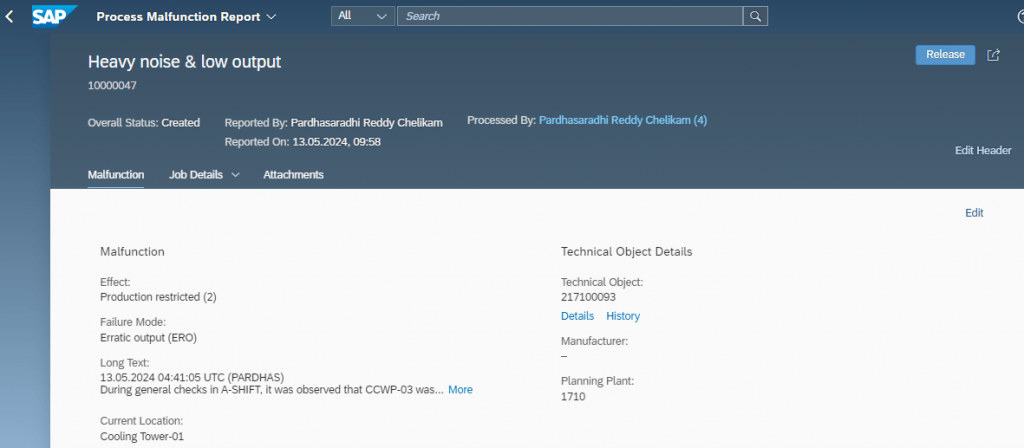
System generates the maintenance order for the malfunction report and assigns the order type as per system configuration.
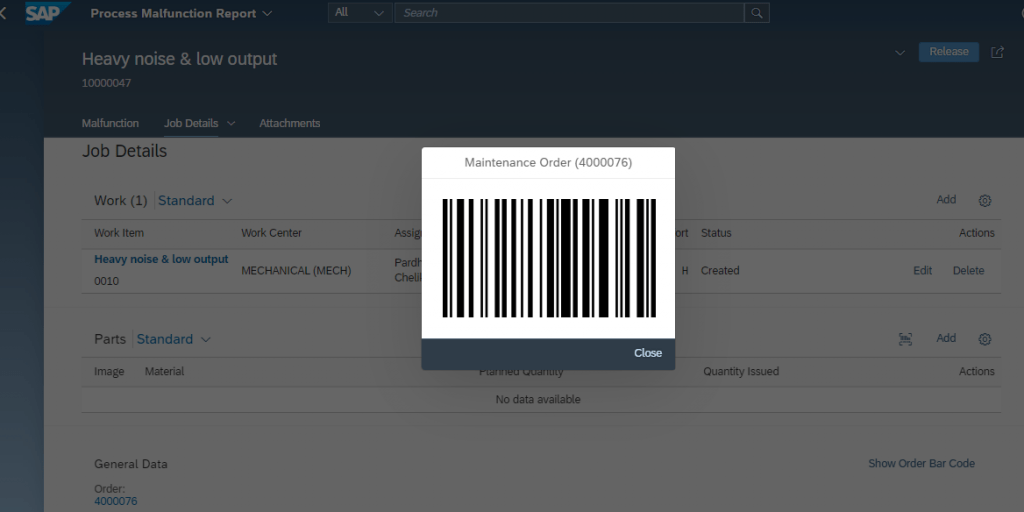
Plan Malfunction Repair Work:
I have planned the repair work with all the resources that are needed,
- Work Items with responsible work center
- Spare parts needed for repair work – Based on the Technical Object BOM system displays the Product Ids, if no BOM exists, we can search the required product IDs and assign to the malfunction report
For Instance, as a lead maintenance technician, I am going to have below operations and assign to respective main work center (Maintenance Technician) and relevant effort details.
- Isolate Power Supply
- Process Clearance -Isolate all Inlet and Outlet valves
- Issue Safety Certificate
- Inspect and replace Tyre Coupling
- Perform alignment
- Enable Power Supply
- Enable Inlet and Outlet valves
- Trial run and capture vibration readings using SPM meter
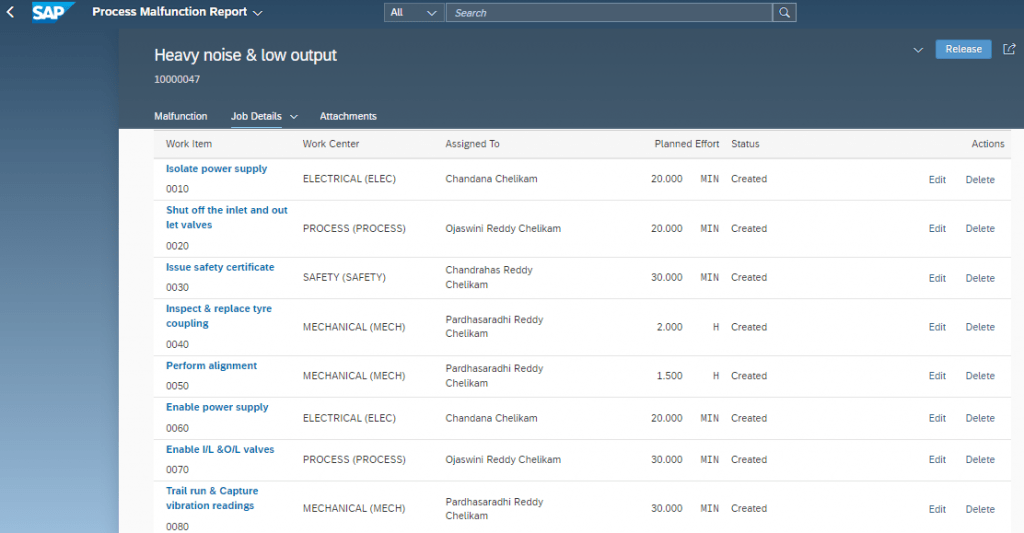
I have chosen below Products for pump repair work,
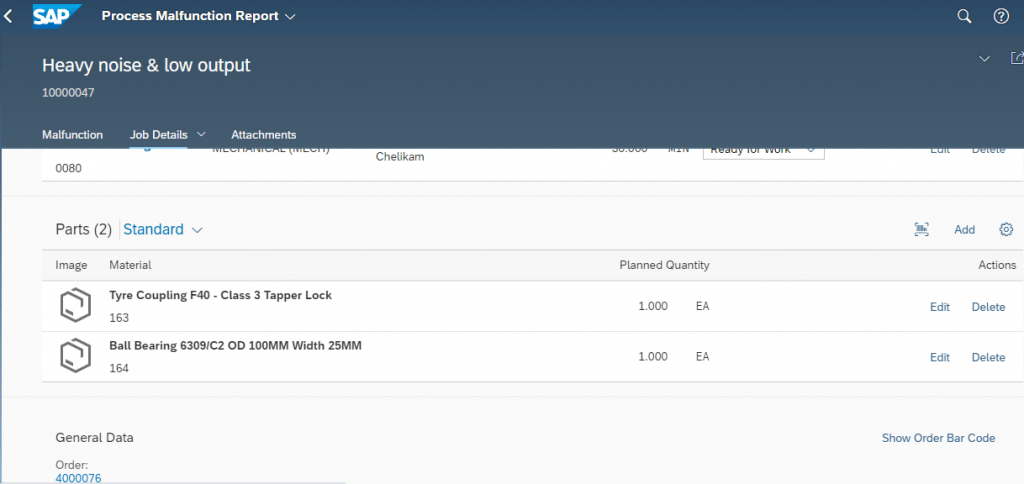
Now I release the malfunction report, then the status of the work item gets updated as “Ready for Work”,
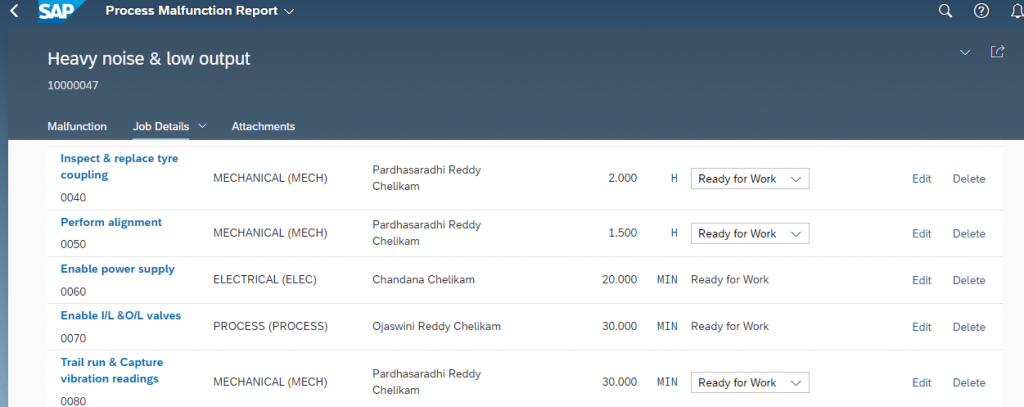
Now, let us view the work order of the malfunction report (Work Order Operations & Planned Cost details) from the malfunction report screen,
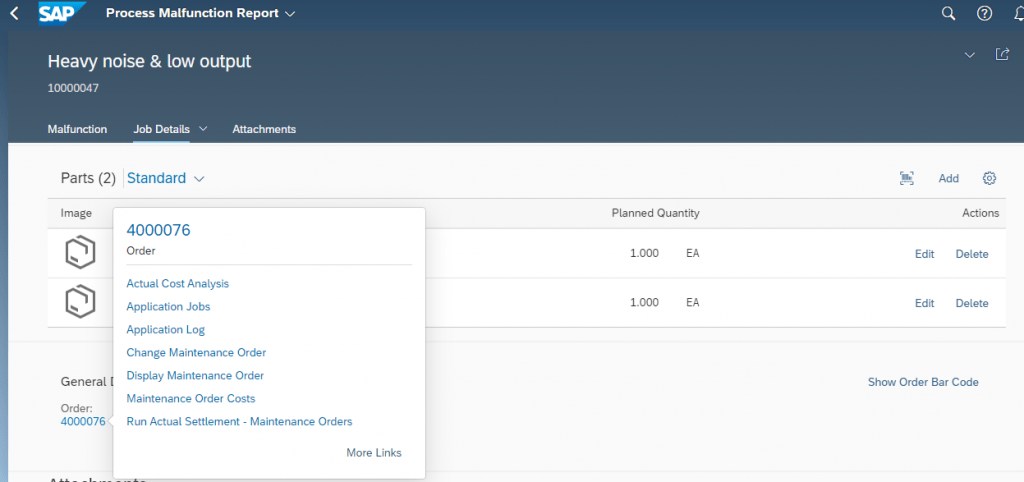
Click on “Display Maintenance Order”
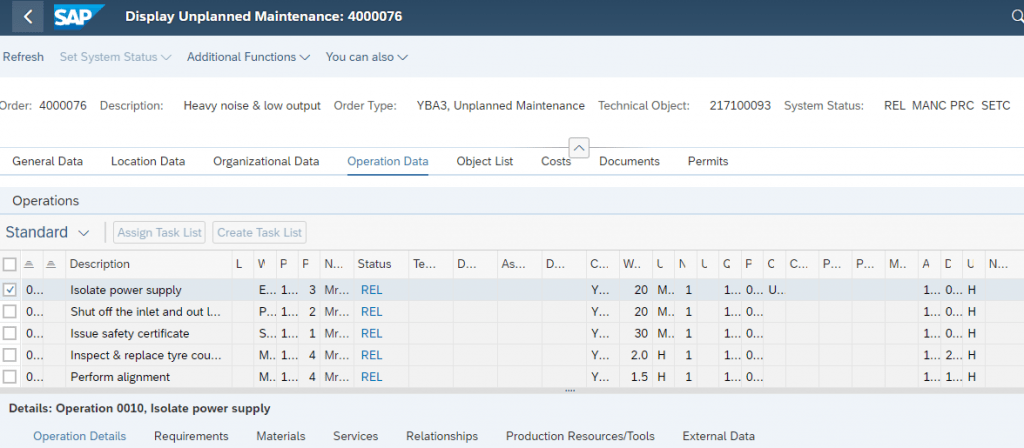
As my business case demands the tracking of spent hours cost of each employee in the work order of the malfunction report, I have set up “Activity Type” and assigned to respective Main Work Center to capture maintenance technician spent hours. System updated the planned cost for Internal Activity, and for the planned products.
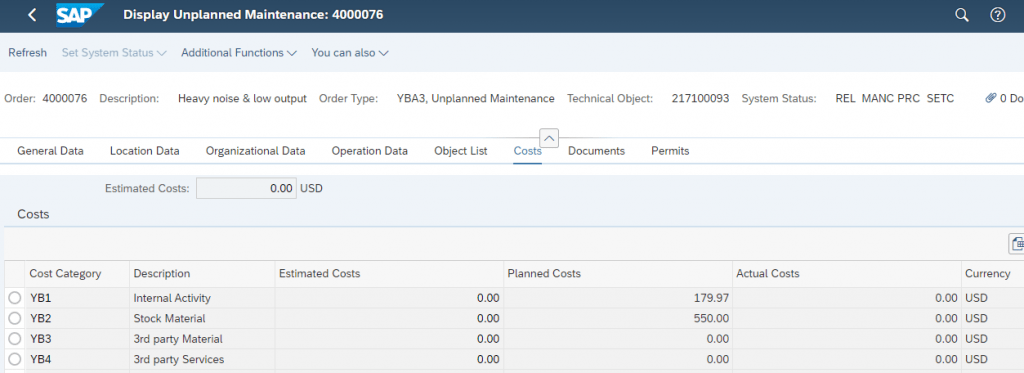
Once the work has been assigned to respective maintenance technicians, each technician can either run the “Manage Malfunction Report” or “Repair Malfunctions-My Job List” to update their respective work item status.
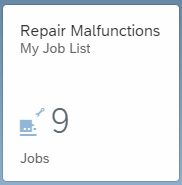
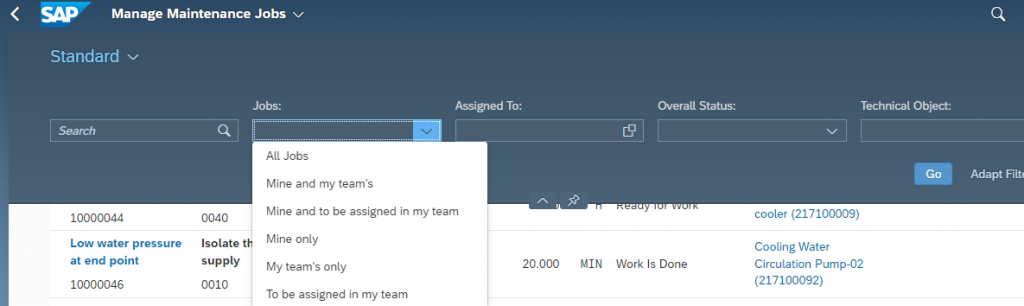
With this “Repair Malfunctions – My Jobs List”, I have got multiple options to select the work items based on Jobs. I have selected “Mine Only” to get all the work items that have been assigned to me.
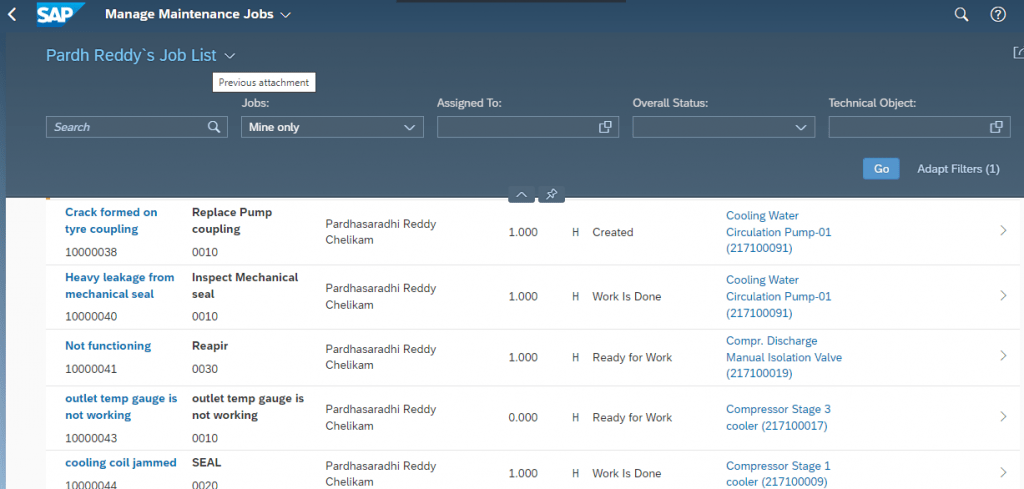
I can process required work item by choosing respective work item.
For instance, I have chosen “Manage Malfunction Report”, where I can narrow down the work items based on Work Centers which were assigned to each work item.
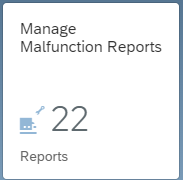
We can have personalized variants with respect to malfunction report attributes, so that it would become handy to process the work items – I have narrowed down the list using Work Center filter criteria.
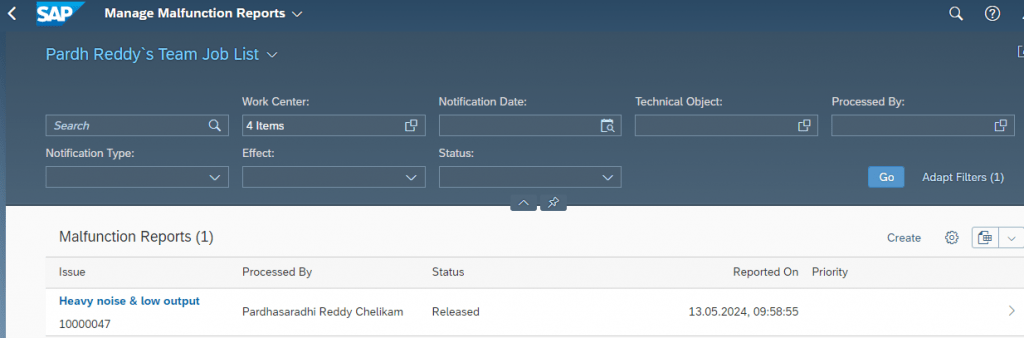
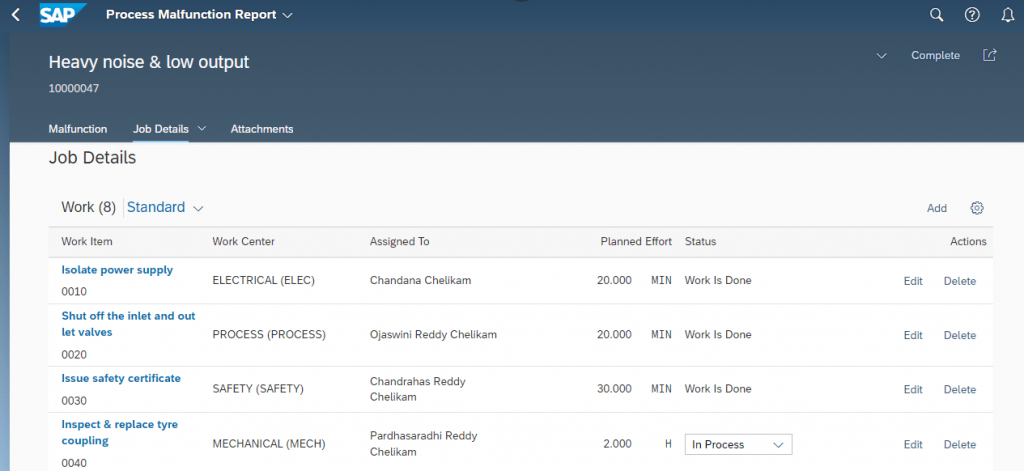
Confirmation of Work Item details:
System has got an option to pause the work if there is a dependency. For instance, I have to get the committed spare parts from engineering stores and that may take a while. So, I have decided to pause the work item.
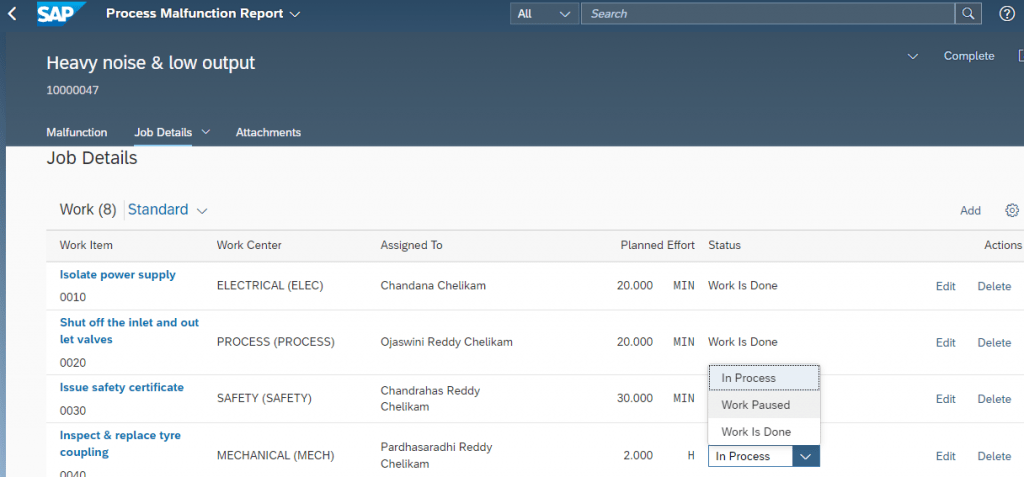
when I paused the work item, system prompted to update the appropriate reason for the pause and to confirm the operation partially.
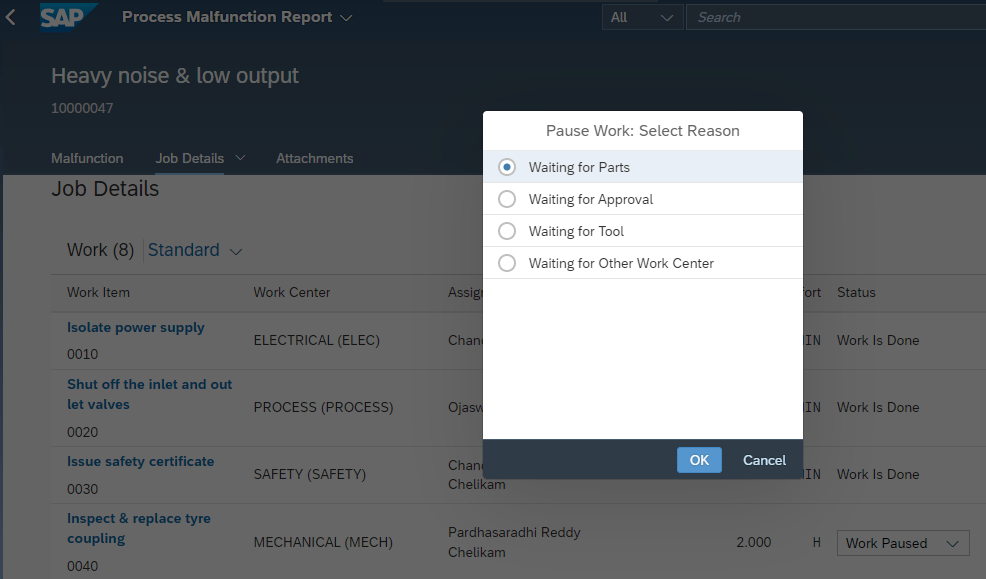
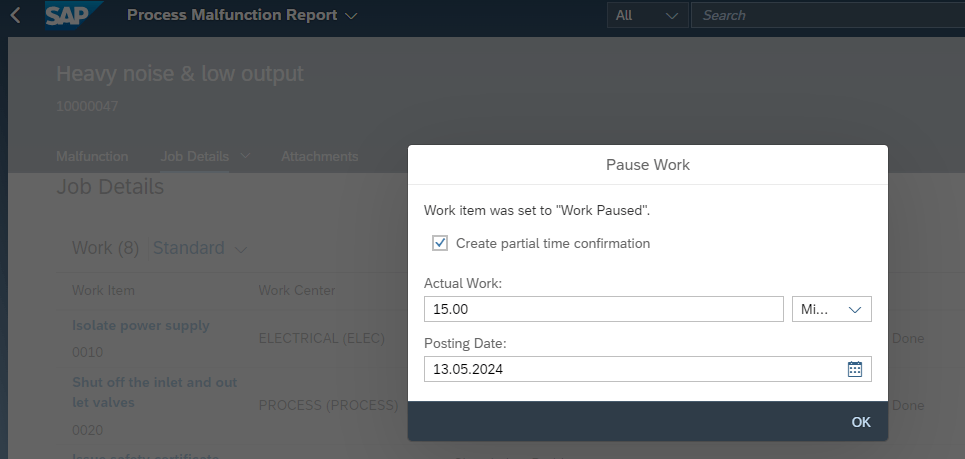
Now, I have received the spare parts from engineering stores. Now I have updated the work item status as “Put In Process” and carried out the work.
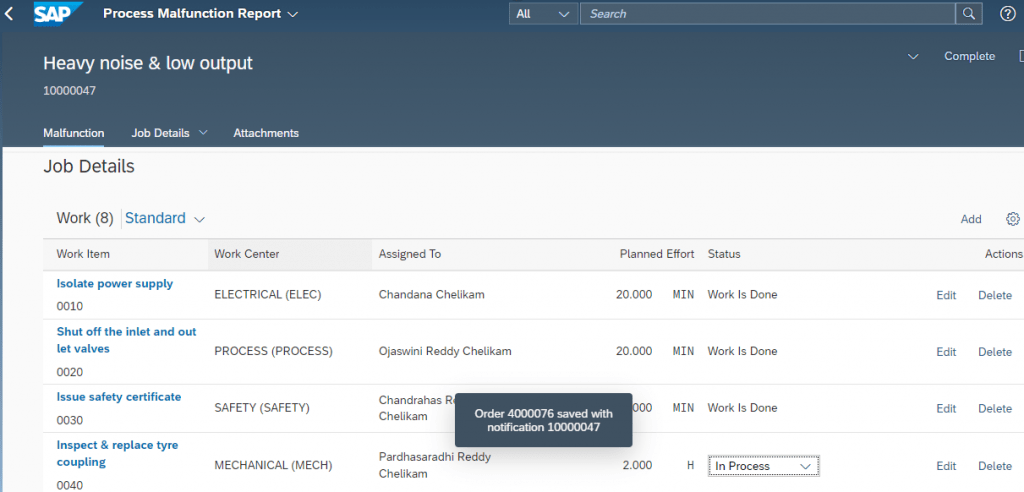
As my work is done at shop-floor, I have updated the work item status as “work Is Done”.
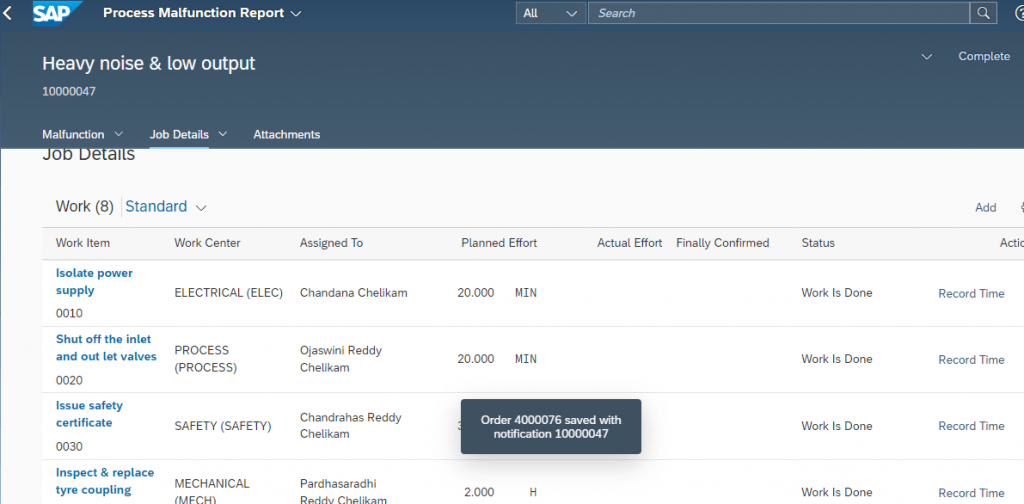
Then, our team has recorded the time that we spent to complete each work item using “Record Time” option.
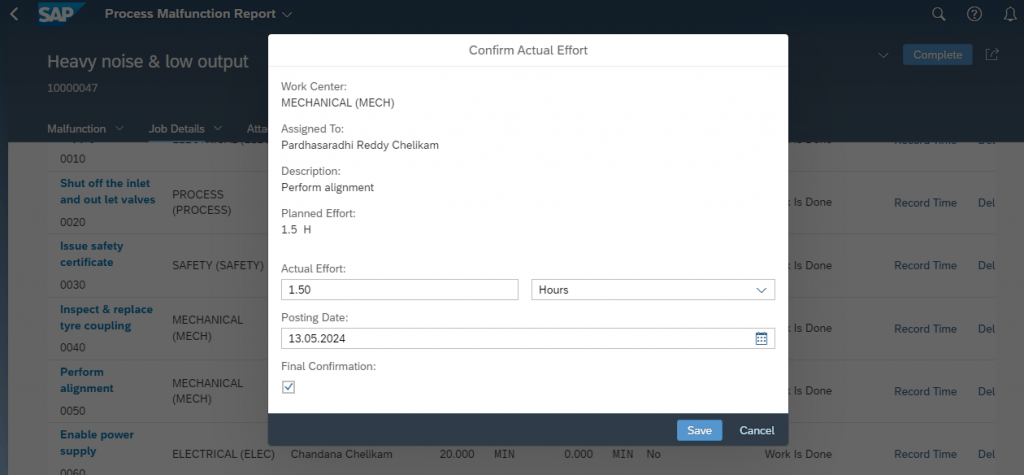
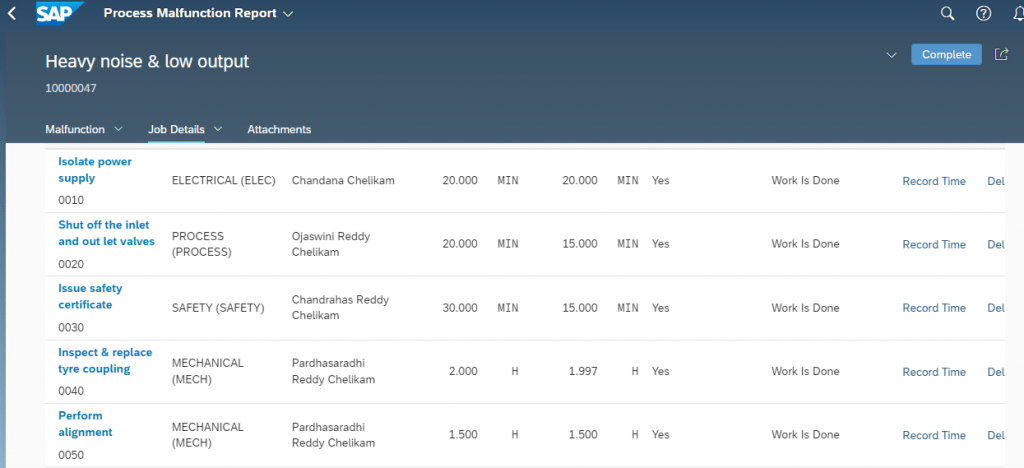
Confirm Malfunction Duration:
My team has captured the spent hours and now I have got to confirm Malfunction Duration, i.e. Malfunction Start Date, Time & Malfunction End Date, Time and specify if the technical object was broken down.
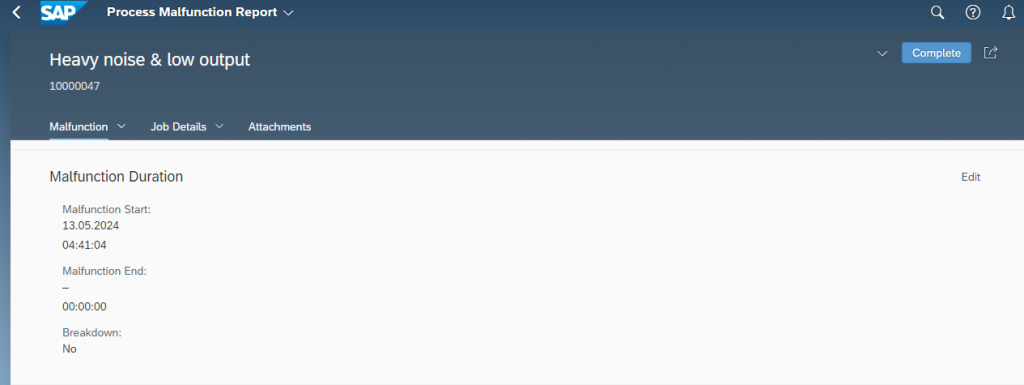
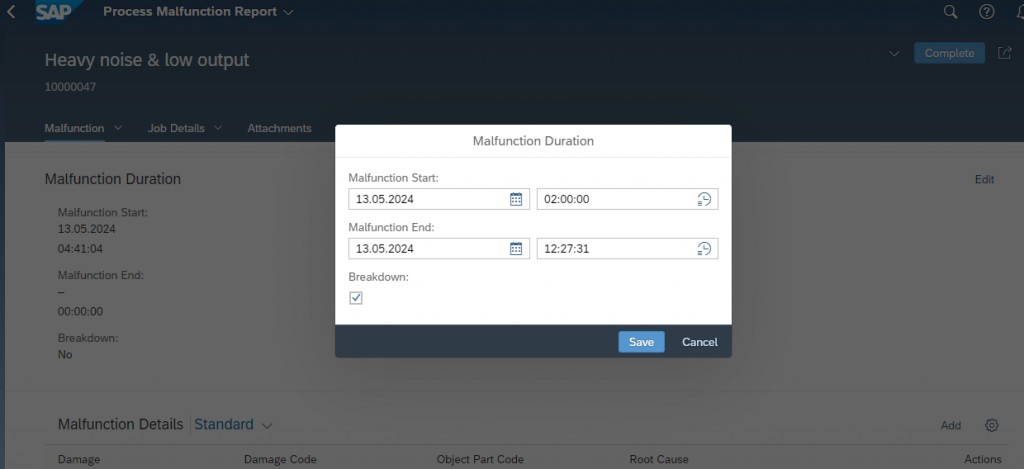
Document the Malfunction Details:
As it is a breakdown, I have got to Specify the affected parts by choosing appropriate damage codes, cause codes and activities that were carried out at shop floor.
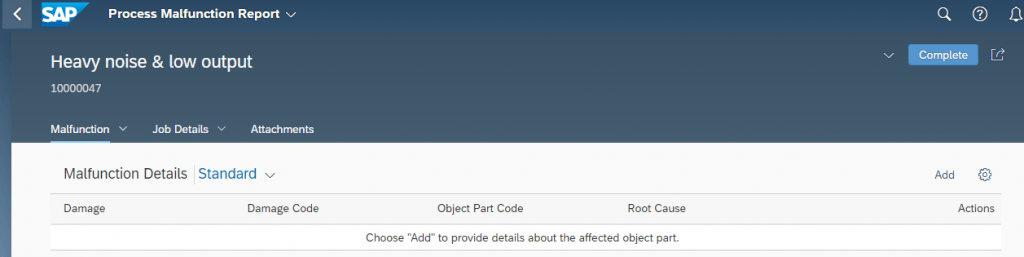
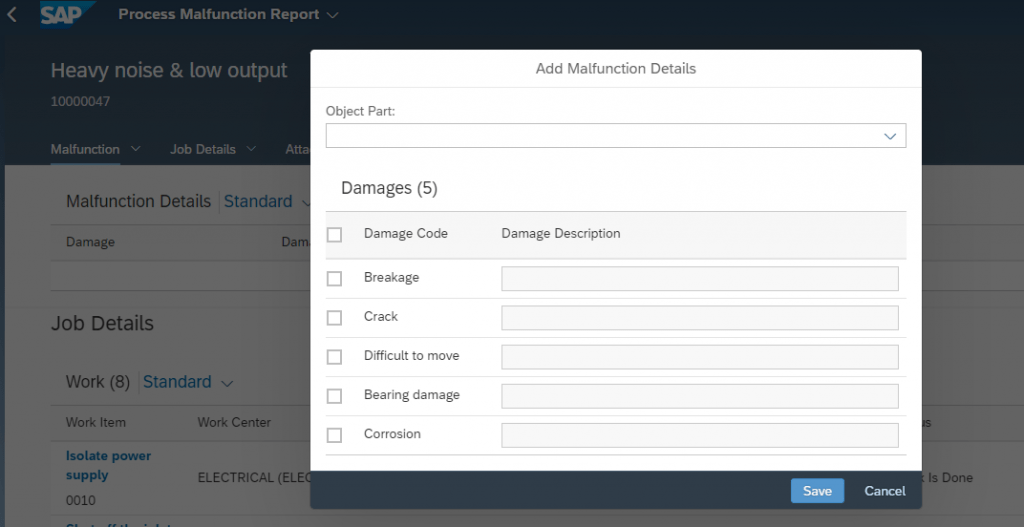
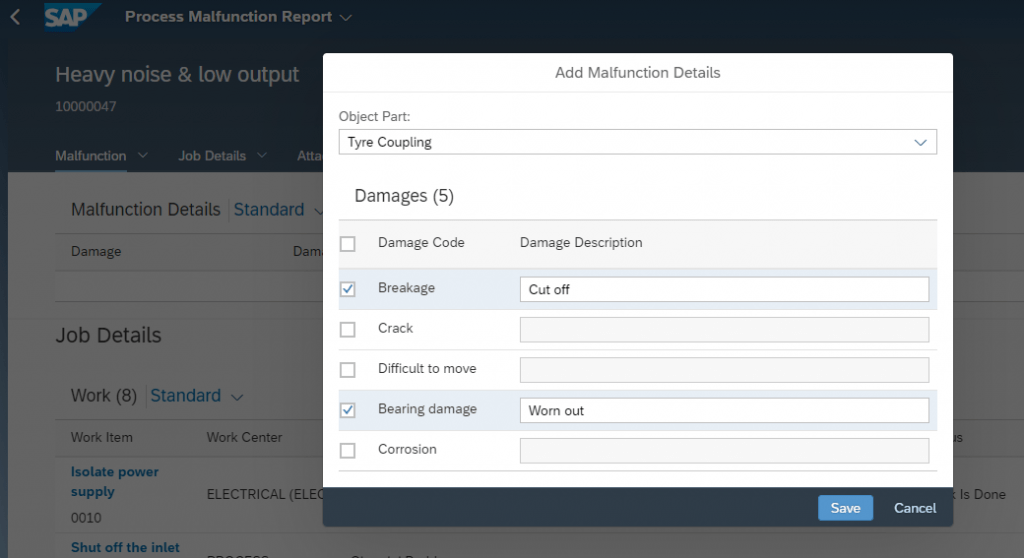
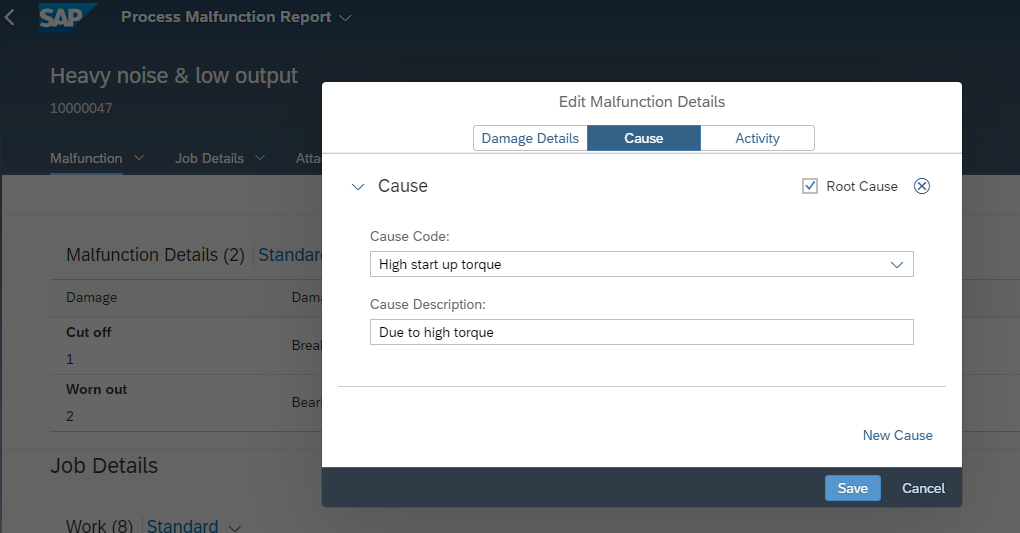

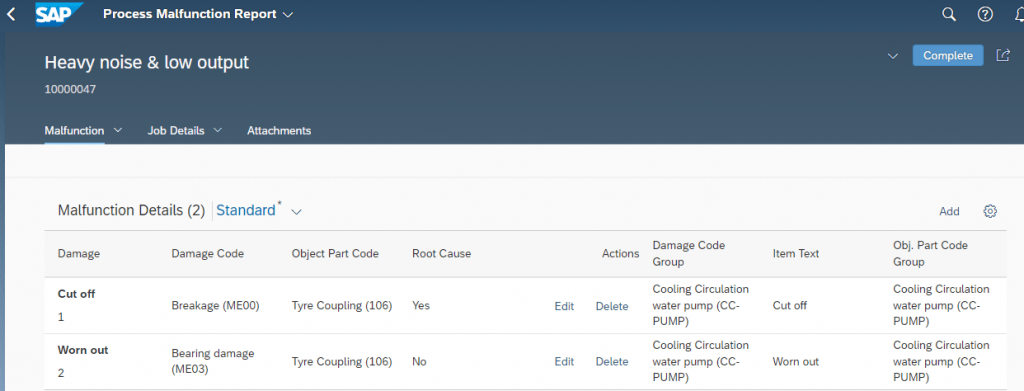
I have captured the root cause details and I have got to complete the “Malfunction Report” by clicking on option “Complete”, then the malfunction report status becomes “Close Report”.
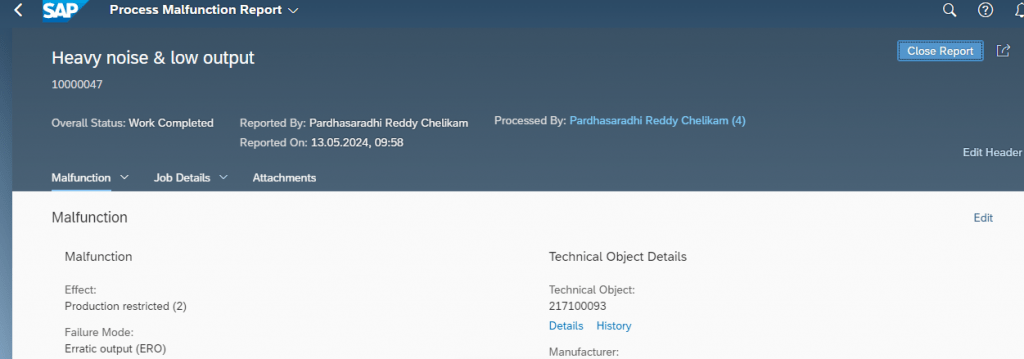
then finally I have closed the malfunction report by clicking on option “Close Report”.
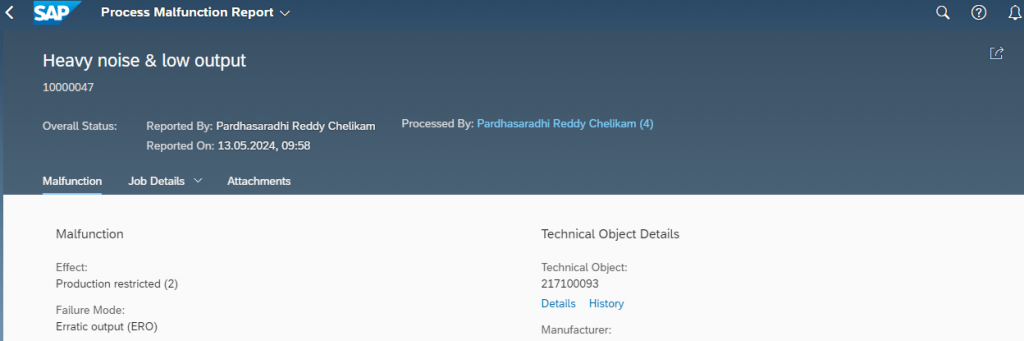
Now, let us look at the maintenance order status and cost details: Order has been technically completed, and operations were confirmed – The actual cost has been updated with respect to material consumption and internal activity (Personal Hours).
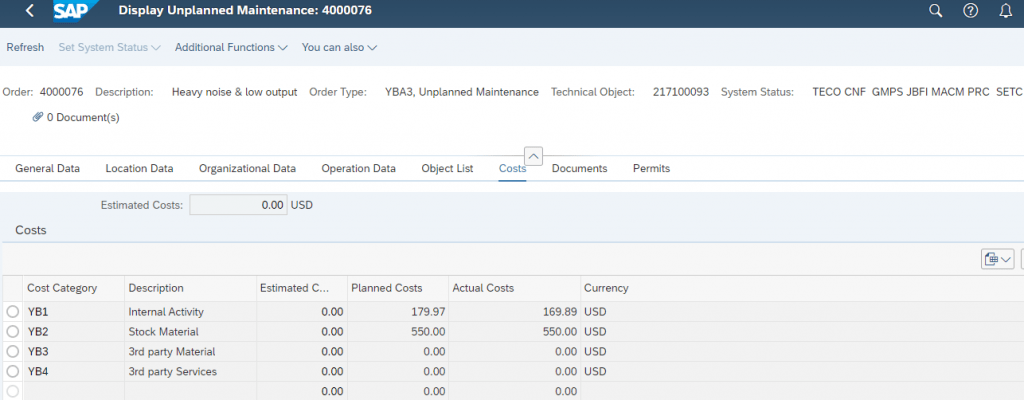
Post completion of the malfunction report, it is obvious that maintenance team analyzes MTTR and MTBF of respective technical object. To get an overview of malfunction details, one should use Fiori App ID F2812.
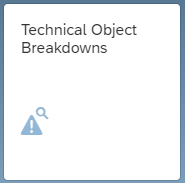
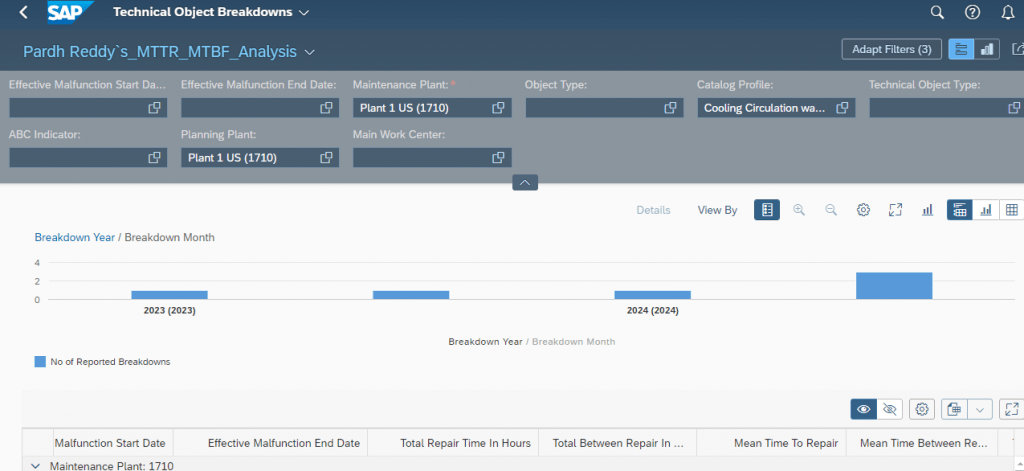
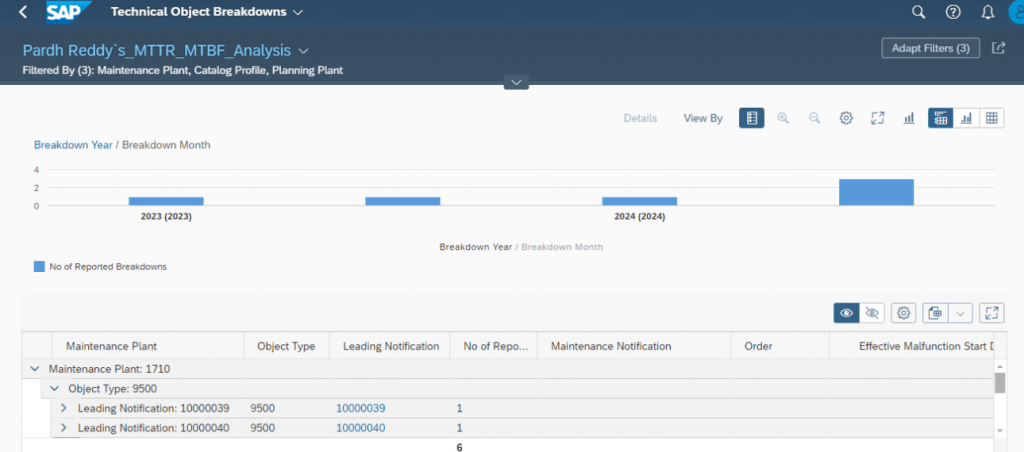
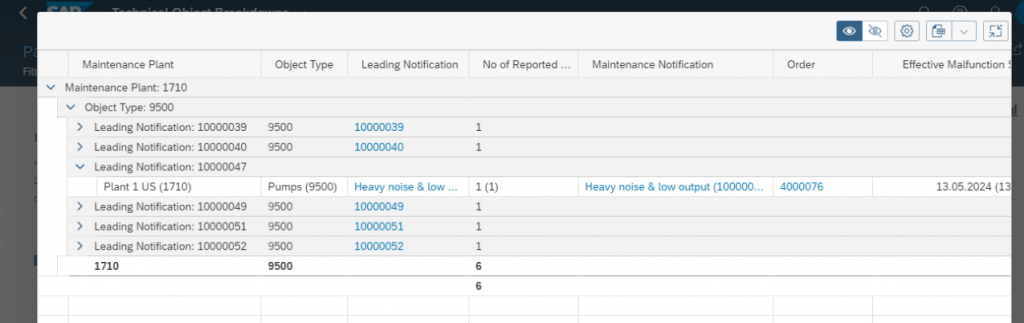
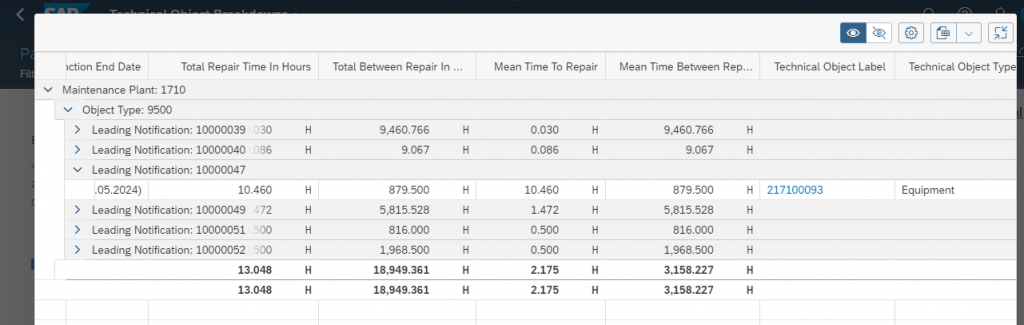
That`s all about genuinely simplified emergency maintenance process in S4 HANA Asset Management.