Objective: The main objective of this is to have a better understanding of the Pricing Procedure configuration setting in SAP S4 Hana.
Purpose of Pricing Procedure:
The purpose of the pricing procedure is combination of different types of charges, like Gross price, freight, discount, surcharges, GST’s etc.
The below steps are followed for Pricing Procedure End to End Configuration
- Set Calculation Schema
- Define Condition Types
- Define Schema Groups for Suppliers
- Define Schema Groups for Purchasing Organizations
- Assign Schema Groups to Purchasing Organizations
- Determine Calculation Schema for Standard Purchase Orders
- Assign new condition Types to Calculation schema
- Assign Schema group supplier to Business Partner
- Validate the Pricing Procedure in Purchase Order
- Maintain Condition Tables
- Define Access Sequences
- Assign the Access Sequence to Condition Types
- Maintain Condition records
1. Set Calculation Schema
Menu path:
SPRO –> IMG –> Materials Management –> Purchasing –> Conditions –> Define Price Determination Process –> Set Calculation Schema – Purchasing
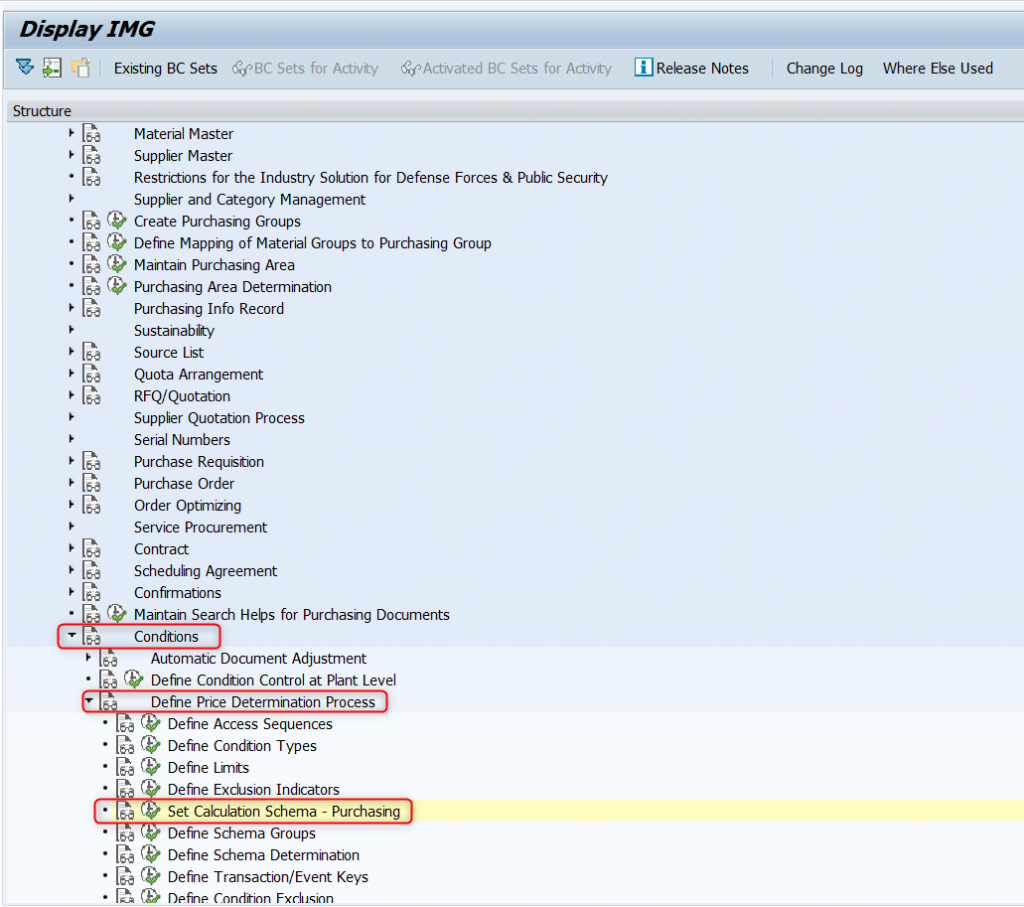
- Click on position
- Enter standard pricing procedure “RM0000” then press enter
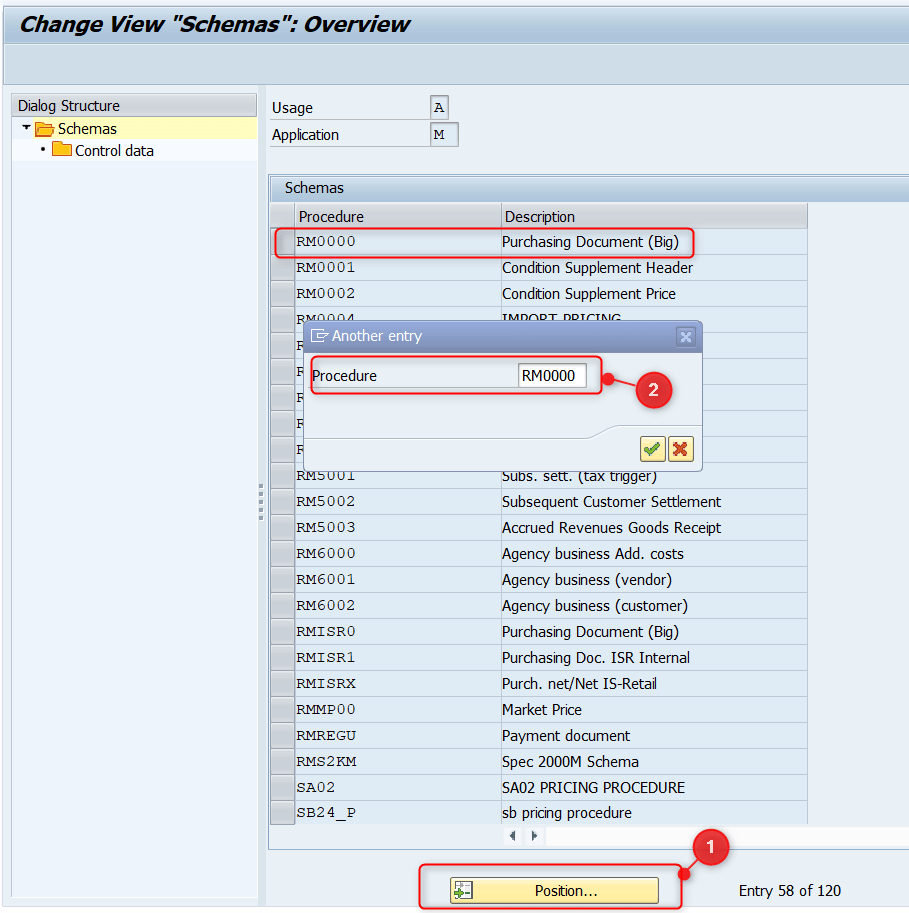
- Select the standard pricing procedure line item
- Click on copy option
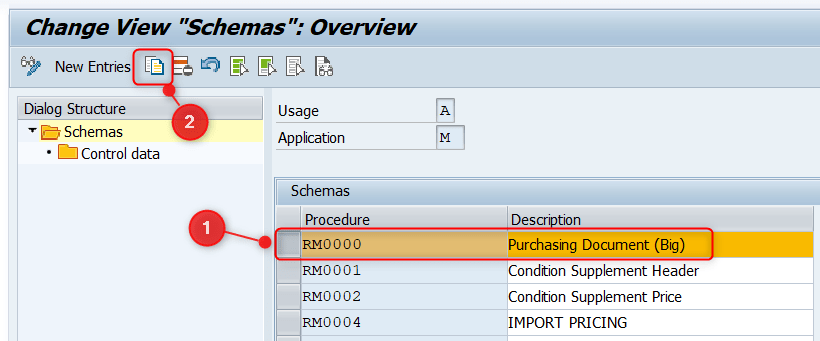
Create own pricing procedure as per the requirement.
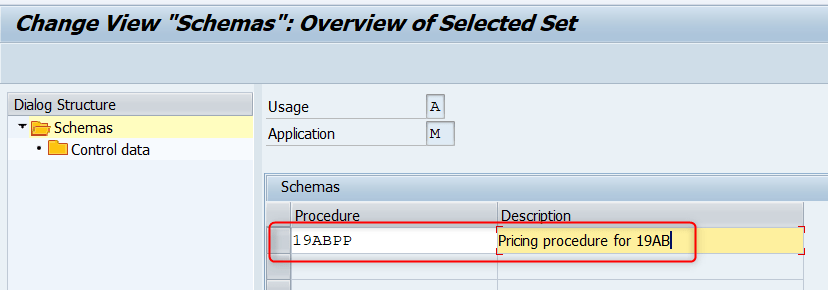
Select copy all
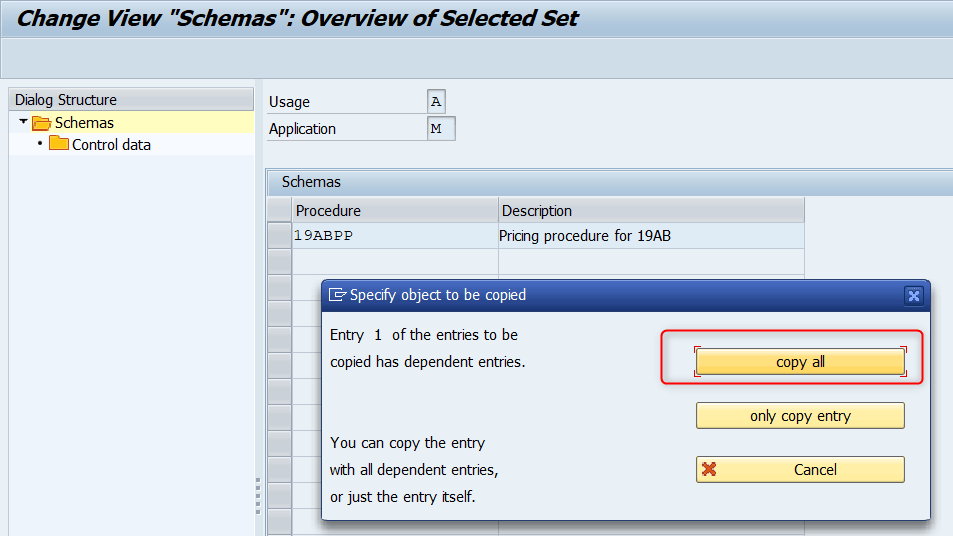
New pricing procedure created

2. Define Condition Types
Menu path:
SPRO –> IMG –> Materials Management –> Purchasing –> Conditions –> Define Price Determination Process –> Define Condition Types –> Set Pricing Condition Types – Purchasing
If you want add SGST & CGST in our pricing procedure, create a condition types
Copy from any of the condition types or new entries
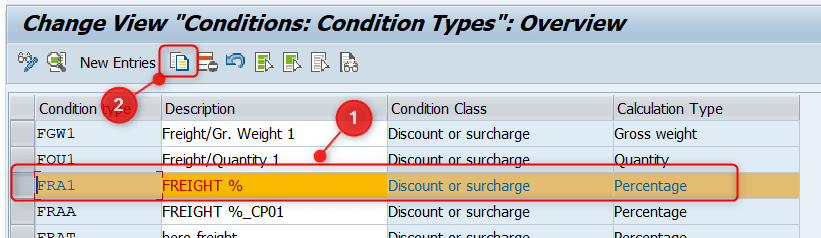
Create new condition type
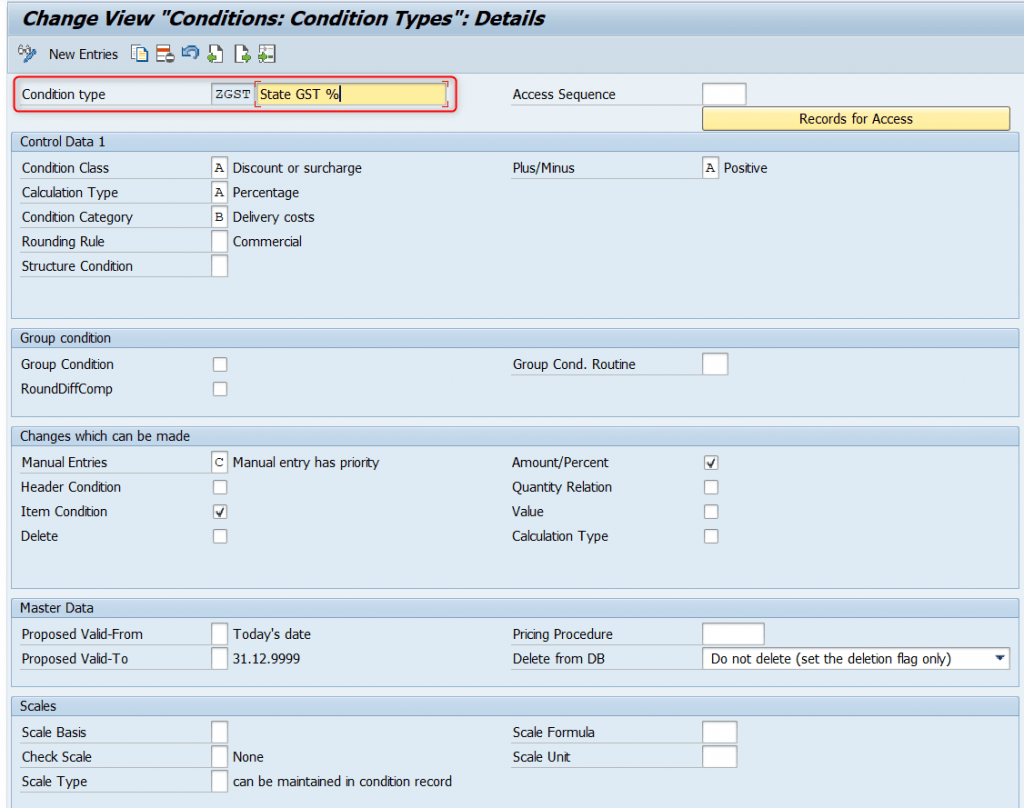
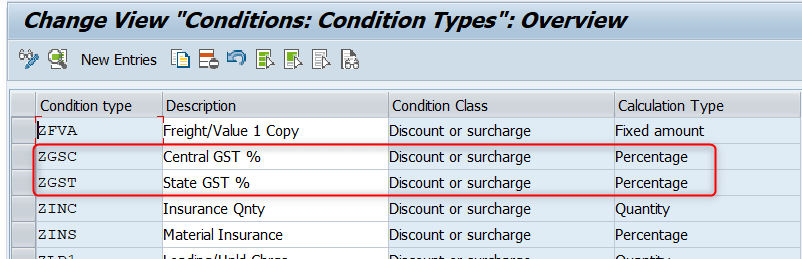
3. Define Schema Groups for Suppliers
Menu path:
SPRO –> IMG –> Materials Management –> Purchasing –> Conditions –> Define Price Determination Process –> Define Schema Groups –> Define Schema Groups for Suppliers
Click on New Entries
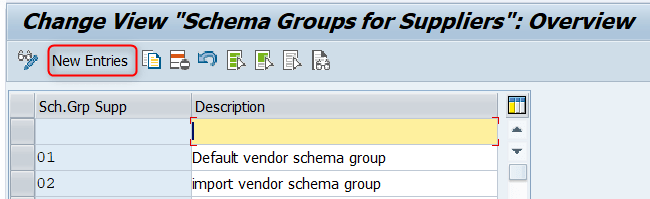
Create new one
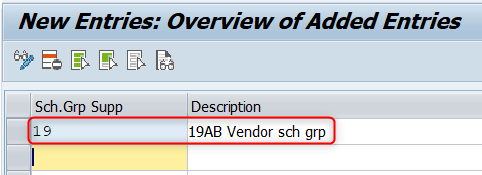
4. Define Schema Groups for Purchasing Organizations
Menu path:
SPRO –> IMG –> Materials Management –> Purchasing –> Conditions –> Define Price Determination Process –> Define Schema Groups –> Define Schema Groups for Purchasing Organizations
Click on New Entries
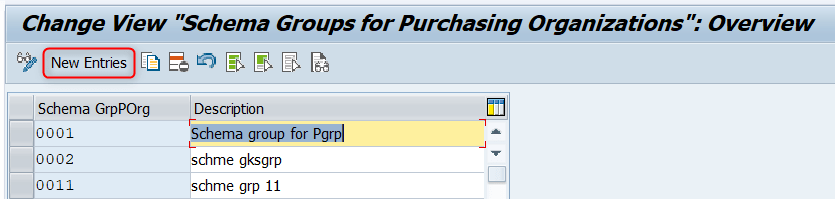
Create new one
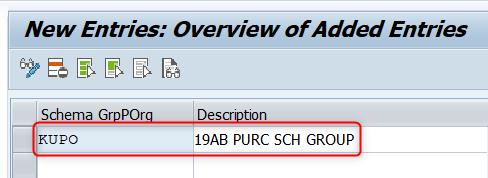
5. Assign Schema Groups to Purchasing Organizations
Menu path:
SPRO –> IMG –> Materials Management –> Purchasing –> Conditions –> Define Price Determination Process –> Define Schema Groups –> Assign Schema Groups to Purchasing Organizations
- Click on position
- Enter actual purchasing organization
- Assign the schema group purchase organization to purchasing organization.
- Press enter and Save.
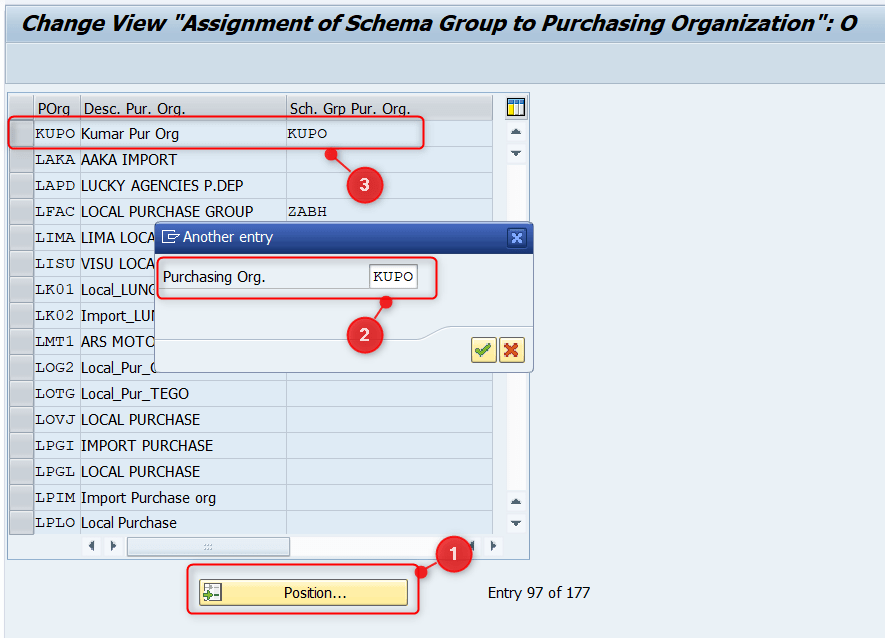
6. Determine Calculation Schema for Standard Purchase Orders
SPRO –> IMG –> Materials Management –> Purchasing –> Conditions –> Define Price Determination Process –> Define Schema Determination –> Determine Calculation Schema for Standard Purchase Orders
Menu path:
Click on New Entries
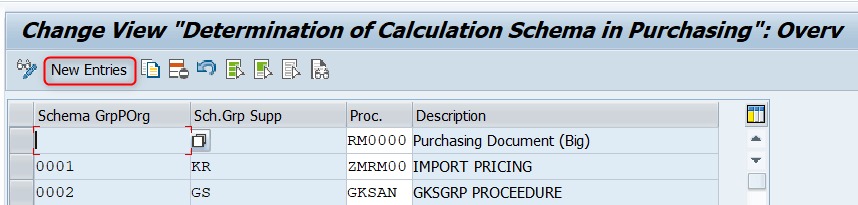
Enter Schema purchasing org
Enter Schema group supplier
Enter new pricing procedure press enter and save.
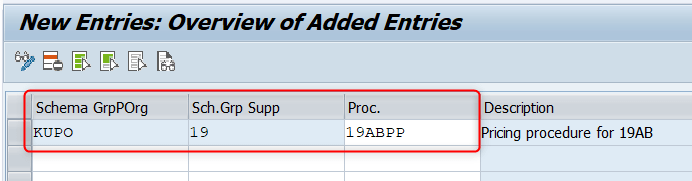
7. Assign new condition types to calculation schema
Menu path:
SPRO –> IMG à Materials Management –> Purchasing –> Conditions –> Define Price Determination Process –> Set Calculation Schema – Purchasing
- Select out pricing procedure
- Select the line item
- Click on control data
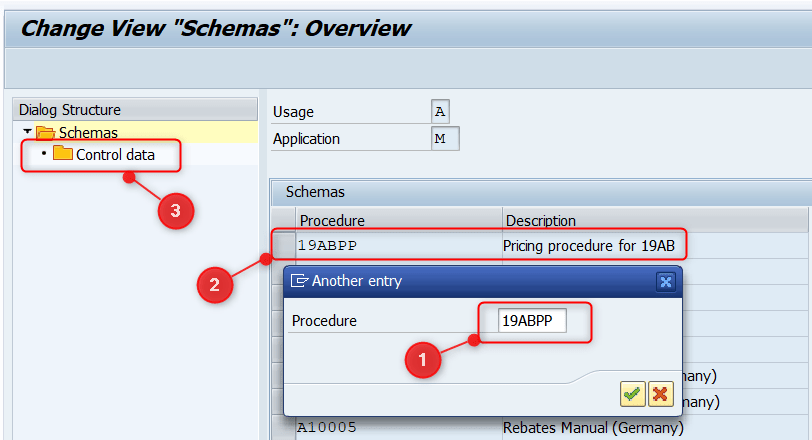
Add new condition types to pricing procedure

8. Assign Schema group supplier to Business Partner
Transaction Code: BP
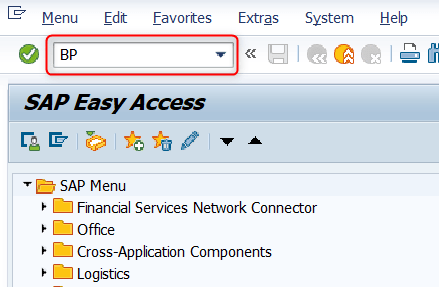
- Click on the open icon
- Enter Business Partner number then continue.
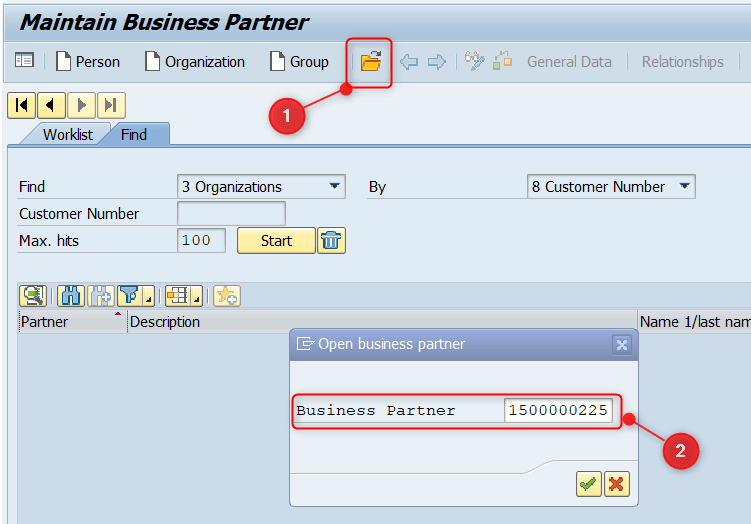
- Choose BP role as Purchasing
- Select Purchasing
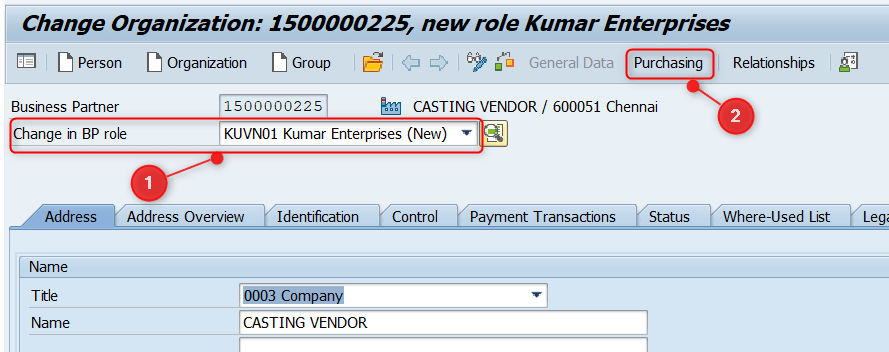
- Select Purchasing Data Tab
- Enter Schema group supplier and Save.
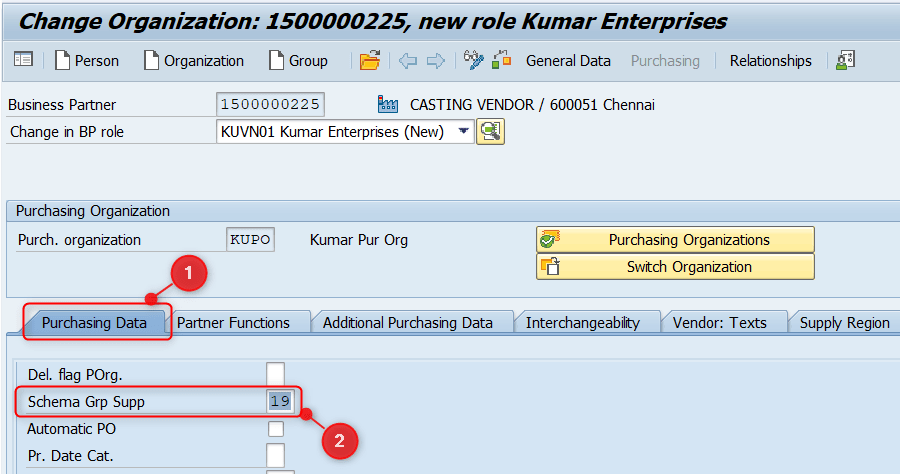
9. Validate Pricing Procedure in Purchase Order
Create New purchase order – T code: ME21N
- Click on Condition tab
- See the new condition types are appeared automatically based on pricing procedure
- Click on Analysis Icon
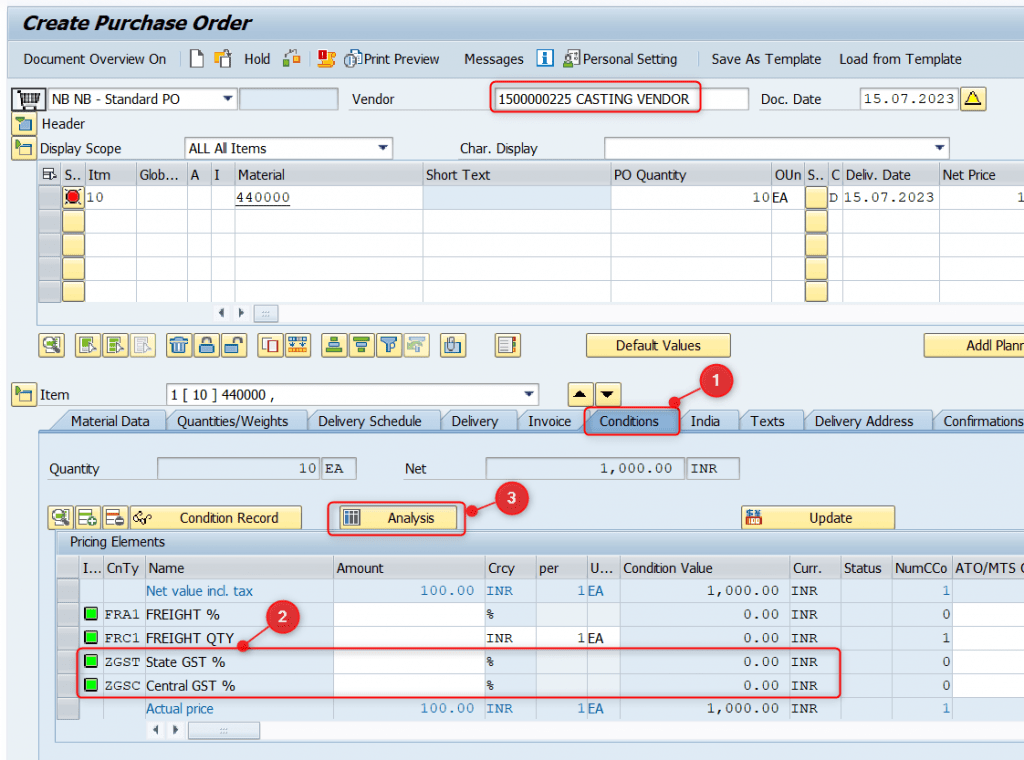
Our New Pricing Procedure was picked successfully.
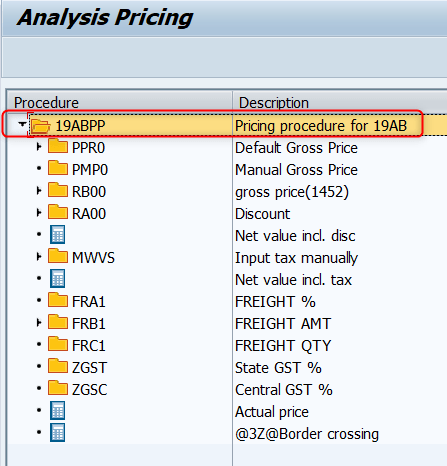
10. Maintain Condition Tables
Menu path:
SPRO –> IMG –> Materials Management –> Purchasing –> Conditions –> Define Price Determination Process –> Maintain Condition Tables –> Create Condition Table
Enter condition table number more than 500 (Any value)
Press Enter
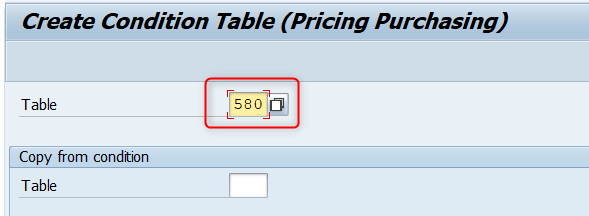
- Which are category required double click from Field catalog side (Left)
- Selected category moved to selected filed side (Right)
- Click on generate icon
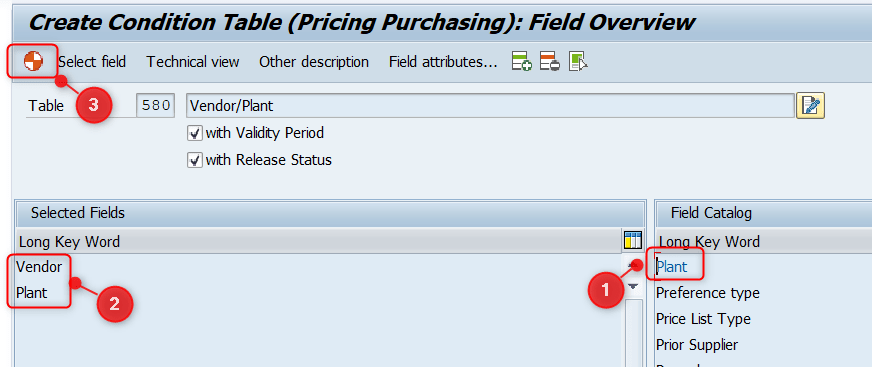
Click on Yes
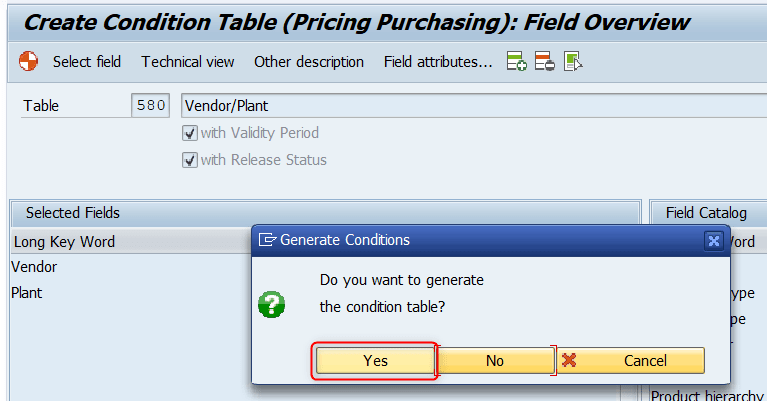
Choose the package and data has been saved
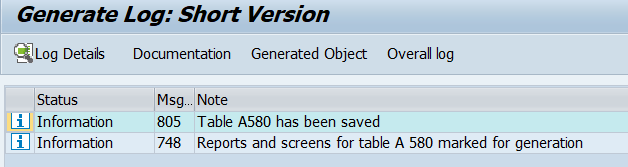
11. Define Access Sequences
Menu path:
SPRO –> IMG –> Materials Management –> Purchasing –> Conditions–> Define Price Determination Process –> Define Access Sequences
Click on New Entries
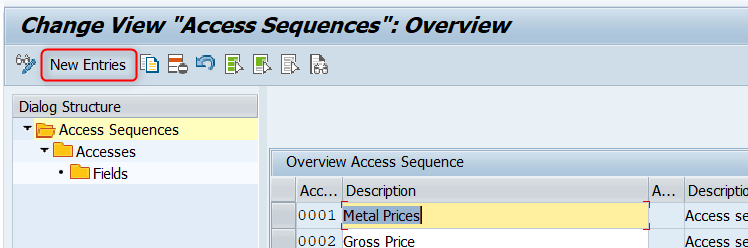
- Create own access sequence
- Then select the line item click on Accesses folder on left side
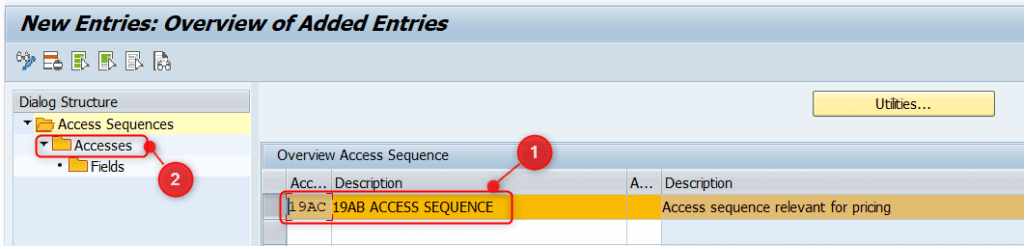
Click on New Entries
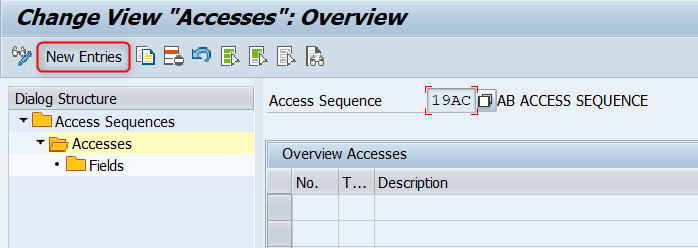
- Enter Condition No and Condition table number
- Select the line item and click on Fields folder on left side
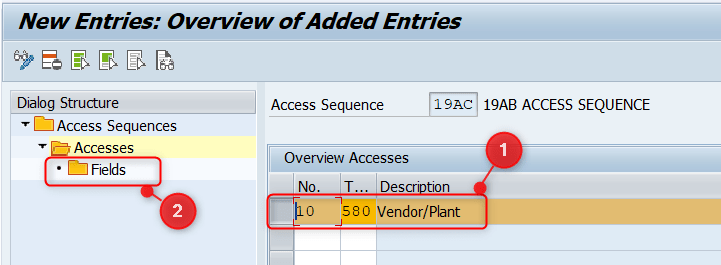
See the filed details and go back then Save the Workbench TR.
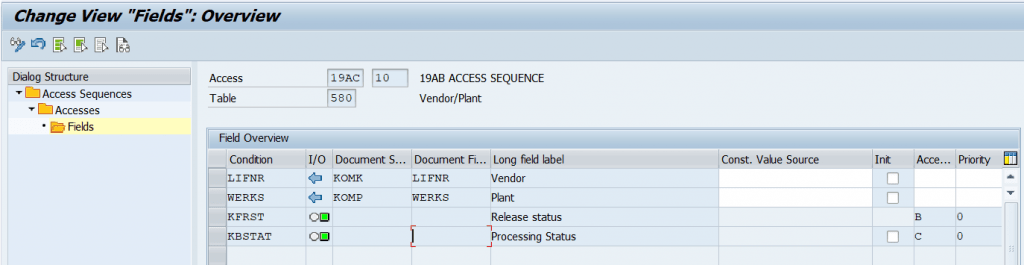
12. Assign Access Sequence to Condition Types
Menu path:
SPRO –> IMG –> Materials Management –> Purchasing –> Conditions –> Define Price Determination Process –> Define Condition Types –> Set Pricing Condition Types – Purchasing
Find our condition types using Position option
Then double click on condition type
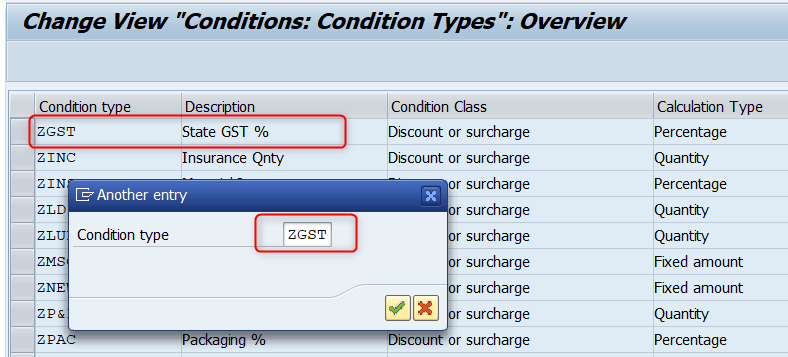
Assign the Access Sequence and Save.

13. Maintain Condition Table (Manual)
Transaction code: MEK2
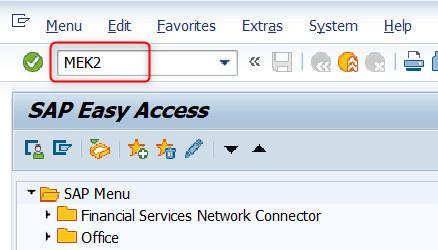
Enter condition type
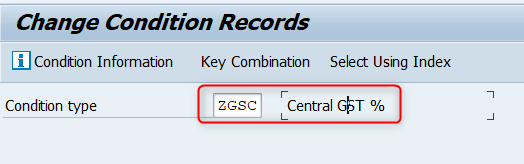
See the combination of condition type and click on execute icon
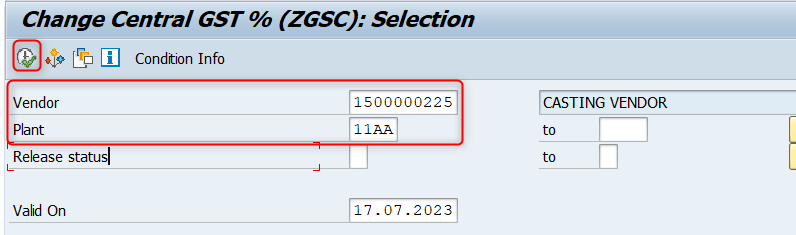
Enter plant and percentage of condition type and Save.
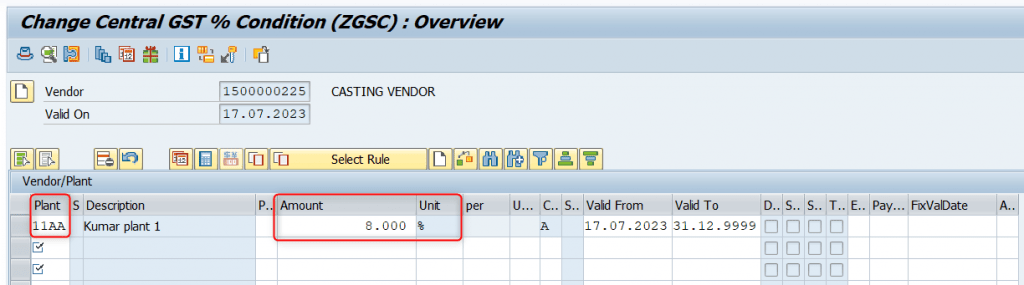
Create New Purchase Order: T Code ME21N
While creation of purchase order, ZGST & ZGSC amount automatically picked from maintained condition table.
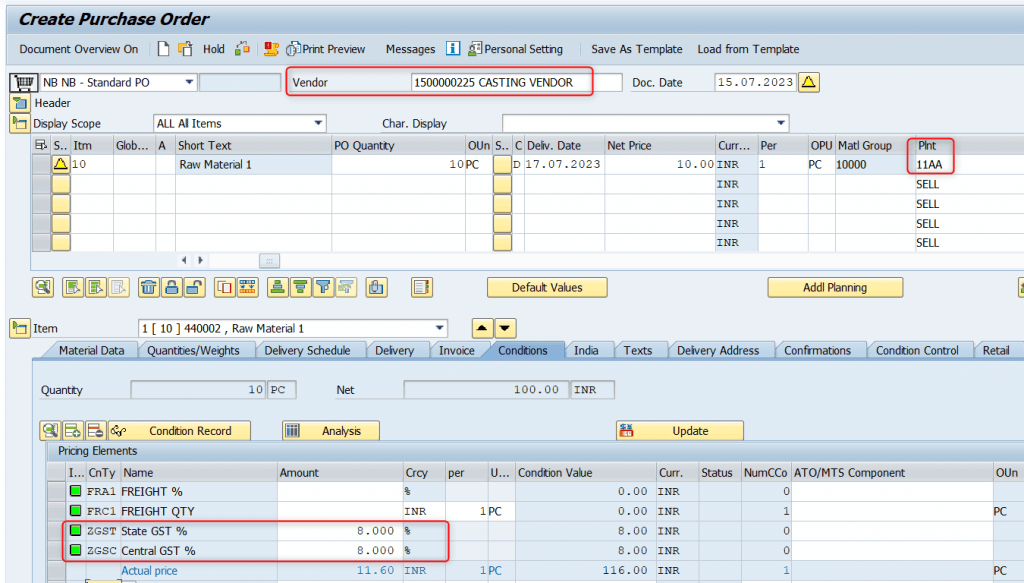
Successfully Configured Pricing Procedure.
The above information is helpful to end to end setting up Pricing Procedure configuration