Introduction:
Quality Notification is created to indicate defect in material at any stage of the work in the plant. Depends upon the details of the defects recorded the solution will be taken by the corresponding department or person responsible. This notification will also act as a record to take the evaluation to know the performance of the material in the various operation and to take right decision with the suppliers to dealt with it.
Overview:
Step1: Create a custom screen with required fields.
Step2: Configure QM Notification custom Iflow link in DMC using Manage web server.
Step3: Create data collection to collect the QM Notification number and save it.
Step4: Create a PPD to pass the values from custom screen to Iflow
Detailed steps:
Step1: Create a custom screen with required fields.
1. Custom screen should be created in Business studio.
2. Add the custom screen in DMC through manage service registry.
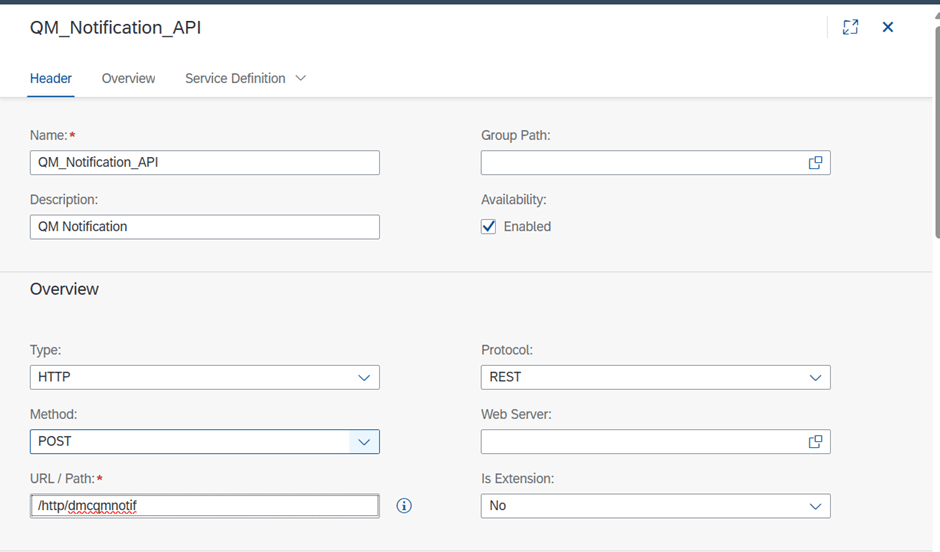
3. Create a button in any POD and assign this custom screen plugin to that button
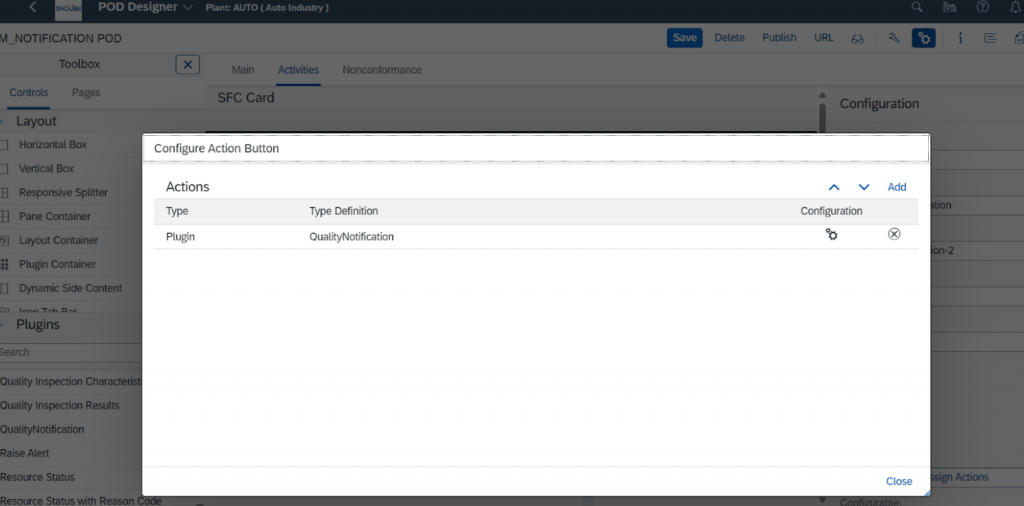
Step2: Configure QM Notification custom Iflow link in DMC.
1. Create a manage web server with the custom Iflow link.
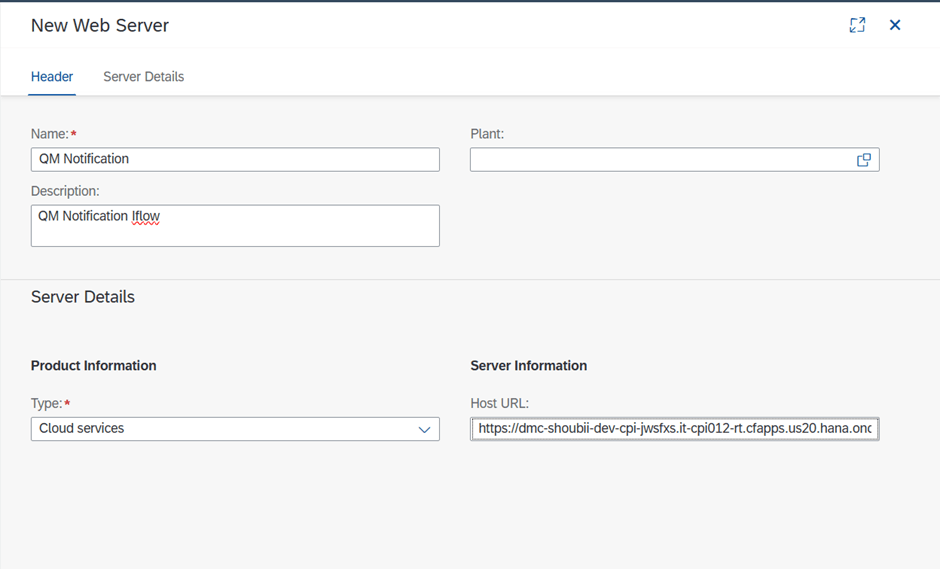
2. Configure web server in manage service registry and assign the schema.
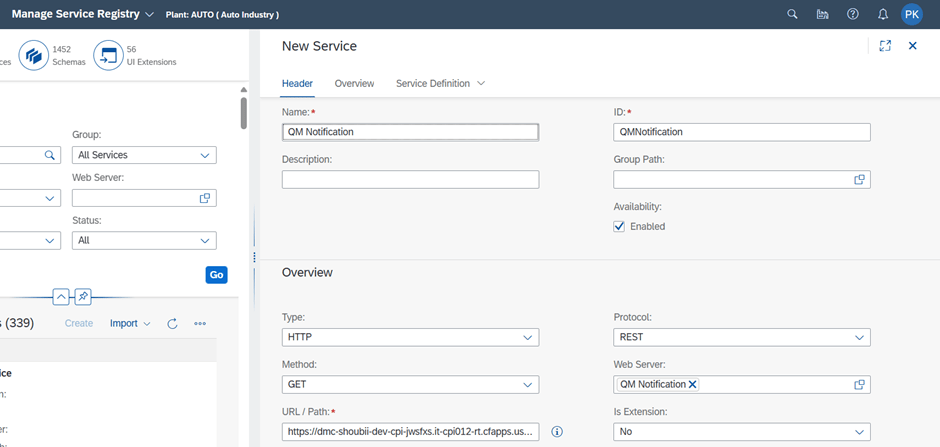
Step3: Create data collection to collect the QM Notification number and save it.
1. Create a data collection group with parameter to collect the QM number created.
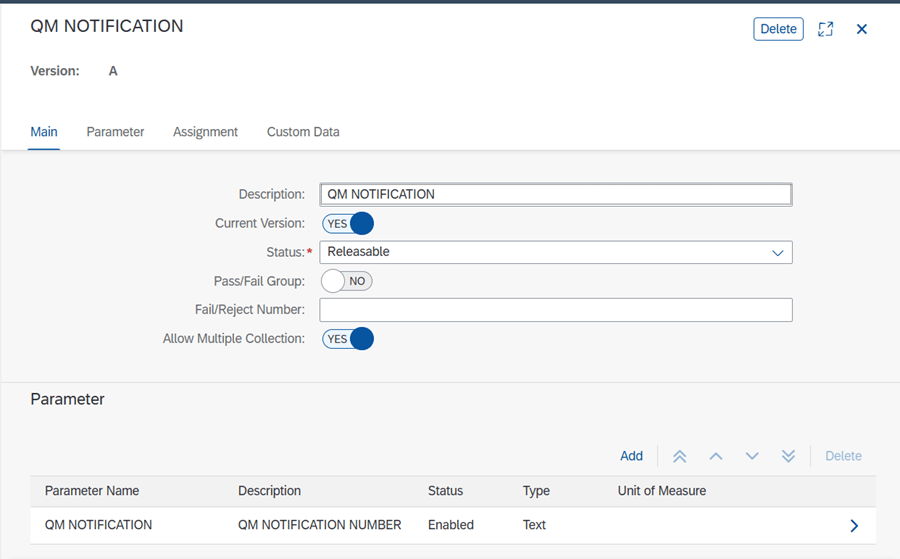
Step4: Create a PPD to pass the values from custom screen to Iflow
1. Select the created service in the production process designer and develop a PPD as per the requirement.
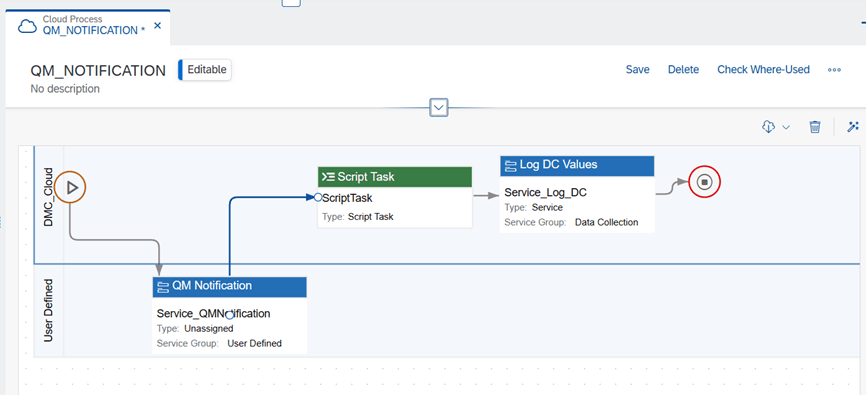
2. Open POD and select the SFC and operation.
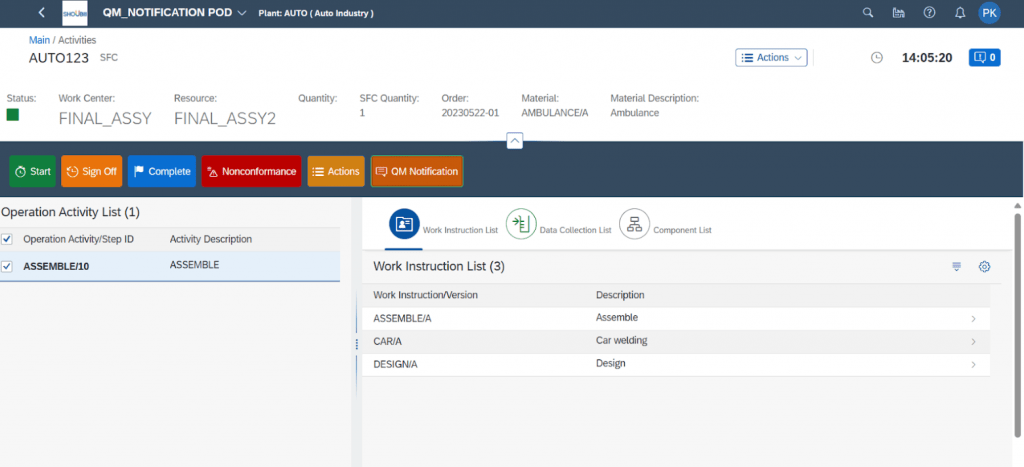
3. Click QM notification button. QM pop up will open along with populated values.
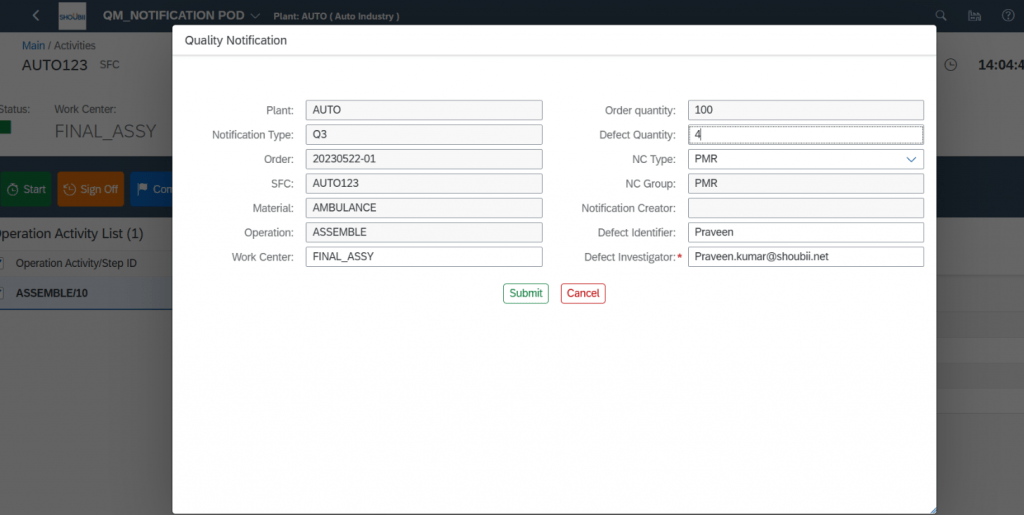
4. Check all values are displayed and click submit. QM notification will create and display in the pop up.
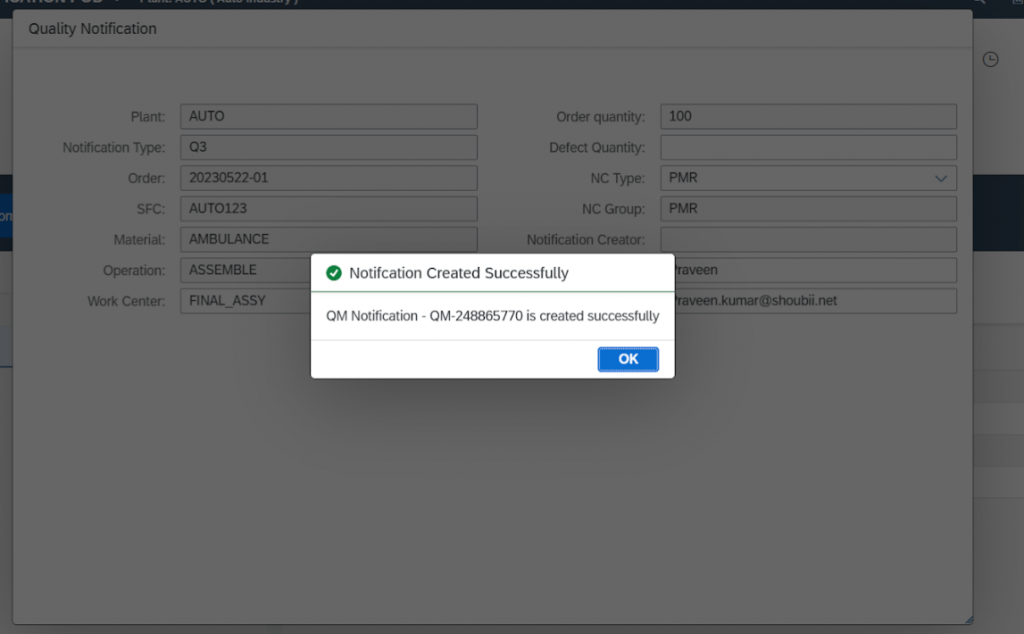
5. Open SFC record. Select the SFC and click Data collection tab.
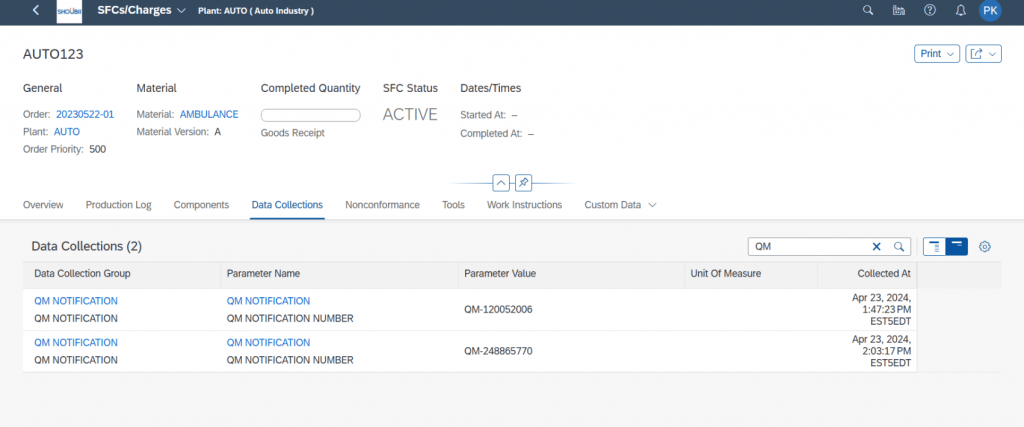
Conclusion:
The Quality Notification serves as a crucial record for identifying material defects during various stages of work in the plant. By documenting defects and involving the relevant departments or responsible individuals, it enables informed decision-making and facilitates communication with suppliers to address any issues effectively.