One of the known issues in PS module is budget availability control for material requirements. In this blog post I would like to share an idea of approach that allows to take material requirements into account during availability check.
Problem
Let’s say there is a project with WBS structure where only level 3 WBS (“Turbine”) is marked as account assignment element. Material requirement is maintained under that WBS element, as depicted below. Materials are booked for valuated project stock. MRP is used to meet the demand.
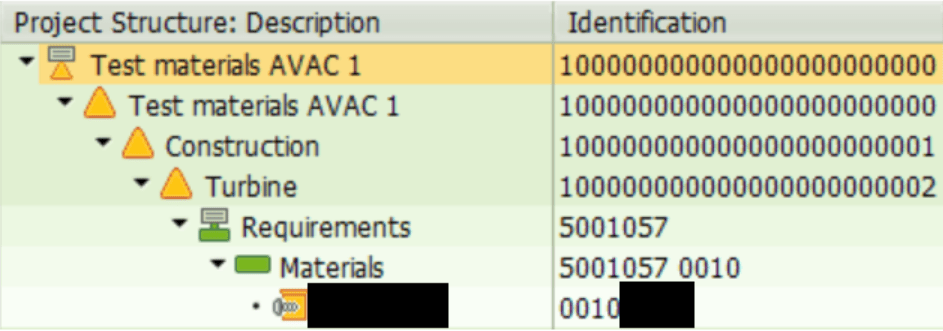
WBS element has budget distributed on it.
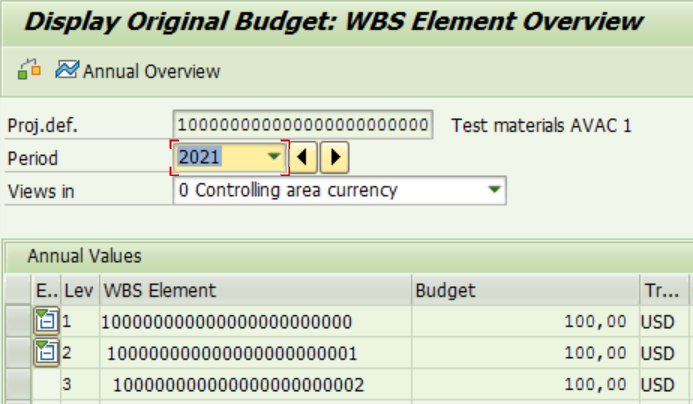
Availability control is activated.
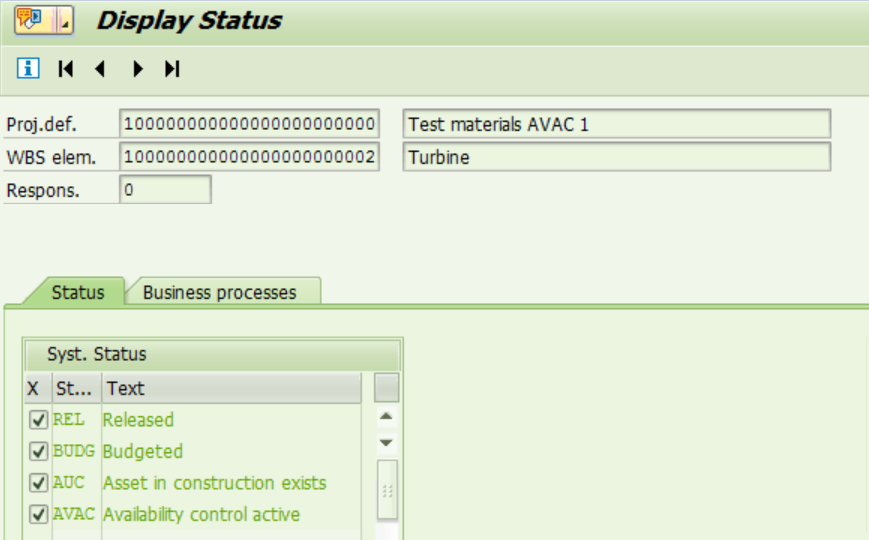
Planned costs exceed the budget (whish is 100 USD, as was shown previously).
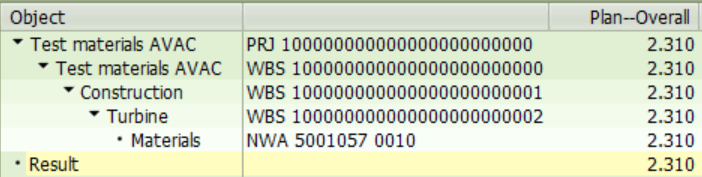
Here I have configured availability control in such a way that system issues a warning message in case budget is exceeded – user would be informed that additional budget has to be requested.
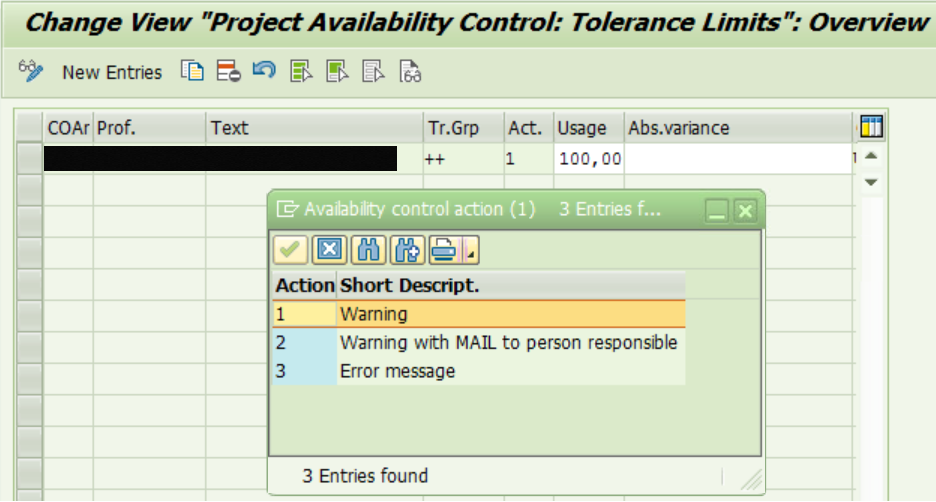
However, system does not issue any kind of message during project save.
This means that planned costs were not interpreted as assigned value and thus were not compared with the WBS budget.
AVAC analysis available in CJ31 could be used in order to investigate and confirm suggestion.
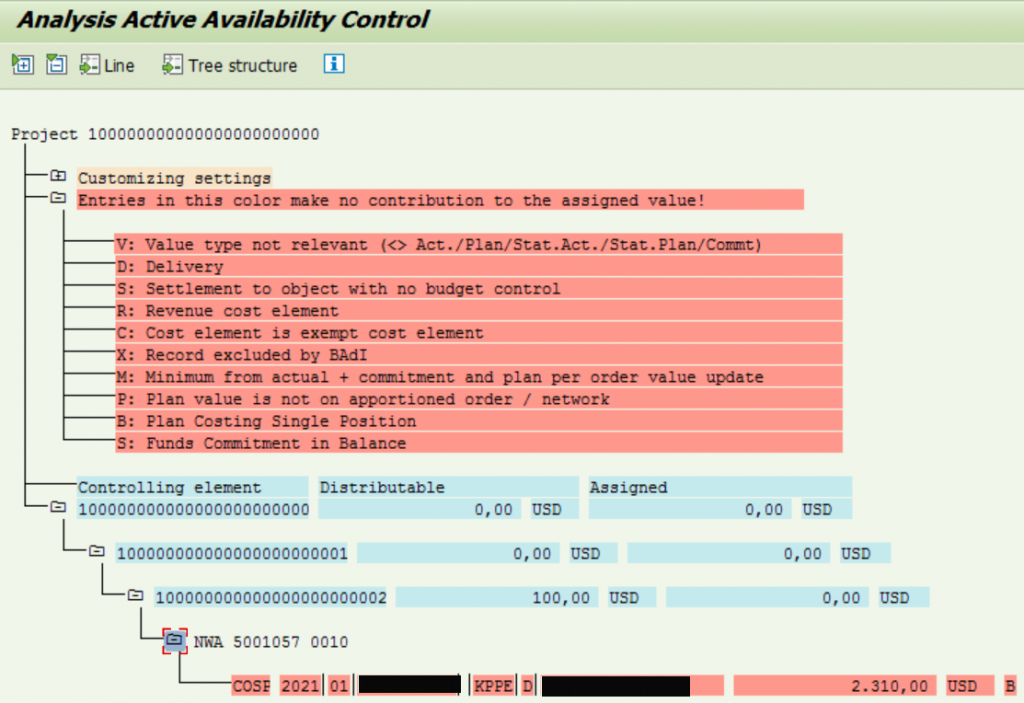
So the availability control does not take materials requirements “reservation for WBS element” into account during project save, which is very disappointing.
The next question you might be asked – when the availability control would hit the alarm if it is not conducted appropriately during project save?
Let’s say that materials would be procured – they are not available in the warehouse. Then the right answer would be that budget availability check would hit when purchasing commitment would be generated.
In case MRP is used you have to keep in mind that commitments are not generated for the purchase requisitions created from MRP. Thus, budget availability check would issue the message only at the time of purchase order creation, which is too late in the most of the cases.
Solution
What you might want to achieve with this solution is the following:
- System should check budget availability during project save including material planned costs as assigned value.
- Obviously you would also want your material planned costs to be displayed correctly in reporting (e.g. S_ALR* reports).
- You would not want to make any kind of development – only customizing of standard functionality should be used.
- Your client’s user shouldn’t have to do any kind of additional time consuming activities – they create material component, save the project and AVAC message must be issued – that’s all.
The main stumbling block here is that system does not take planned costs lines from material component into account. Thus, you have to use some other kind of planned costs.
The first idea that comes up is to use overheads for planned costs. Overhead lines would be considered during budget availability check and are calculated automatically on network save – it fits above requirements.
Therefore, you could apply 100% percent planned cost overhead for each network activity, created for materials planning. However, that would double planned costs. Thus you would have to simultaneously apply -100% overhead using another cost element, which would be excluded from budget availability check using AVAC customizing.
The picture would look in the following way:
- Planned costs, cost element A; $100, not considered by AVAC (standard behavior)
- Overhead +100%, cost element B; $100, considered by AVAC
- Overhead -100%, cost element C; -$100, not considered by AVAC (customizing)
Therefore, budget availability control would compare $100 of overhead (which is equivalent to amount of planned costs) with WBS budget, which is correct.
In reporting, total amount of planned costs would equal $100, because lines 2) and 3) would collapse.
No development and no additional actions for users are required.
Customizing
1) First thing that has to be done – cost elements for overheads should be created.
You would have to create separate cost elements for +100% and -100% overheads.
Cost element category 41 should be used.
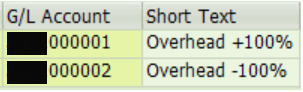
2) Maintain calculation base under Project System – Costs – Automatic and Periodic Allocations – Overhead – Costing Sheets – Define Calculation Bases Referring to Cost Element and Origin
In the sample customizing below cost element group which includes all cost elements used for materials is maintained.
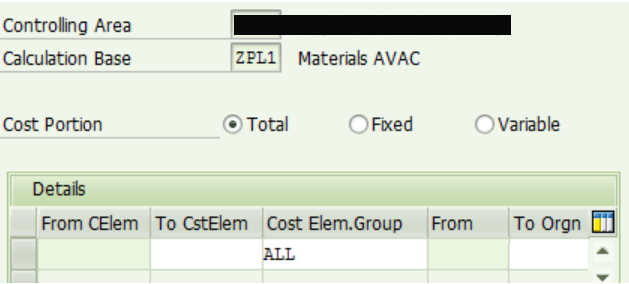
3) Maintain percentage based overheads under Project System – Costs – Automatic and Periodic Allocations – Overhead – Costing Sheets – Define Percentage Overhead

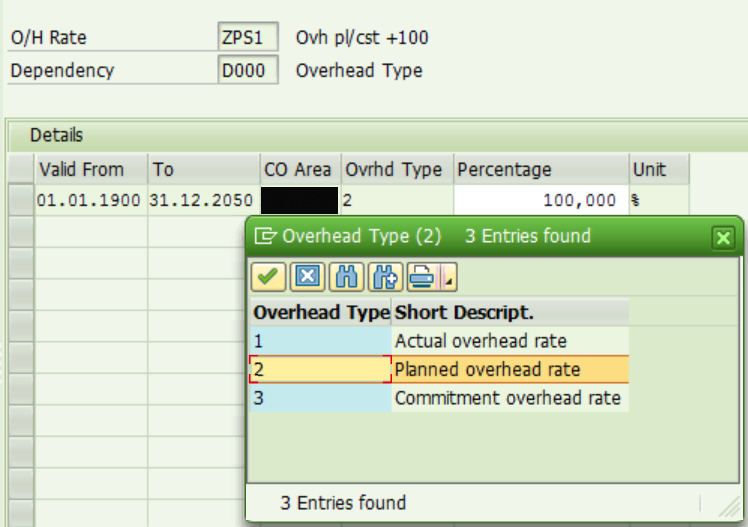
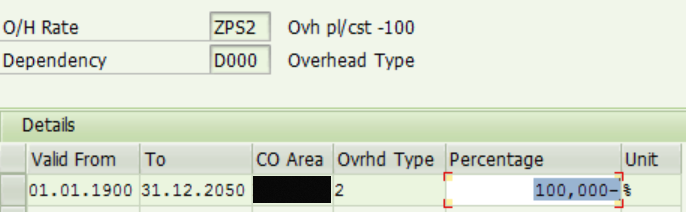
4) Maintain credits under Project System – Costs – Automatic and Periodic Allocations – Overhead – Costing Sheets – Define Credits
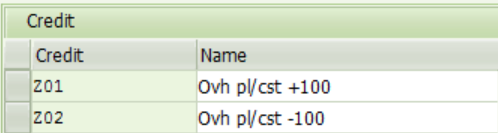
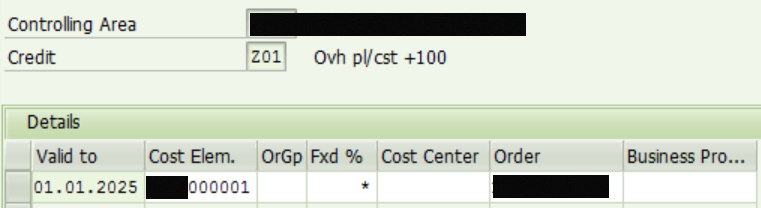
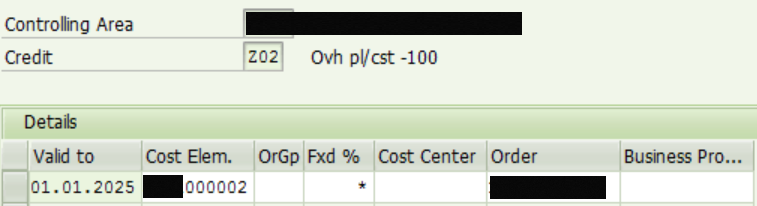
5) Maintain calculation schema under Project System – Costs – Automatic and Periodic Allocations – Overhead – Costing Sheets – Define Costing Sheets


6) Exclude cost element for -100% overhead under Project System – Costs – Budget – Specify Exempt Cost Elements

7) Maintain costing sheet in valuation variant under Project System – Costs – Planned Costs – Automatic Costing in Networks/Activities – Costing – Define Costing Variants
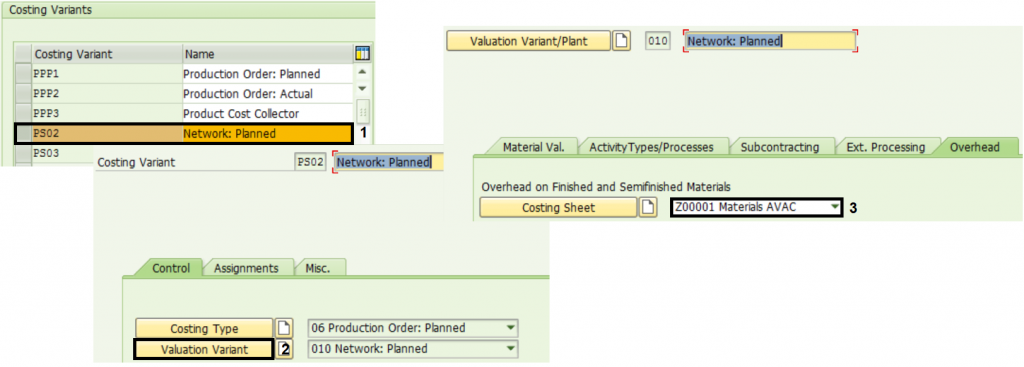
8) Overhead, configured in previous steps, should be applied only for network activities, which are used for material planning. Therefore, costing sheet should be maintained only on such network activities. For other network activities costing sheet must be empty. This could be achieved using substitutions (OPSN).
Simulation
After customizing steps are implemented system applies overhead during network costing.
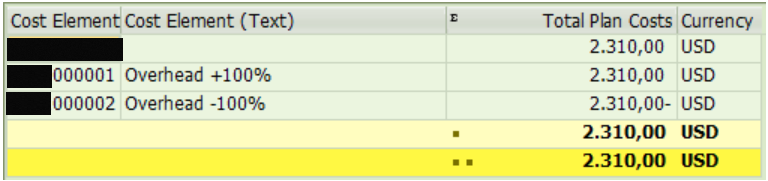
System issues warning message during project save.
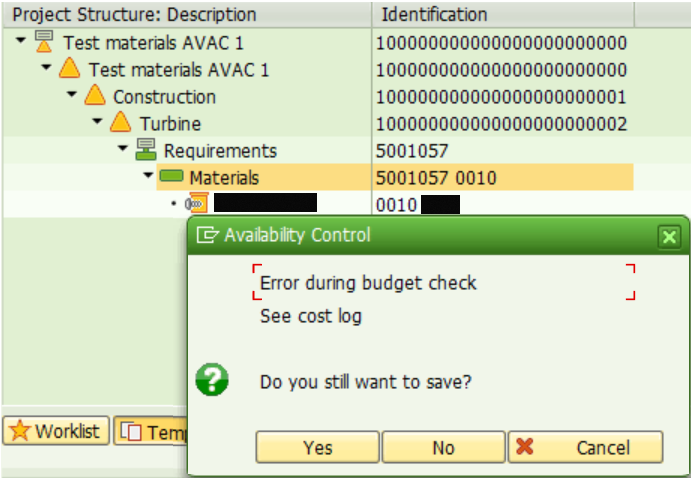
Status “Budget insufficient” is set on superior WBS element.
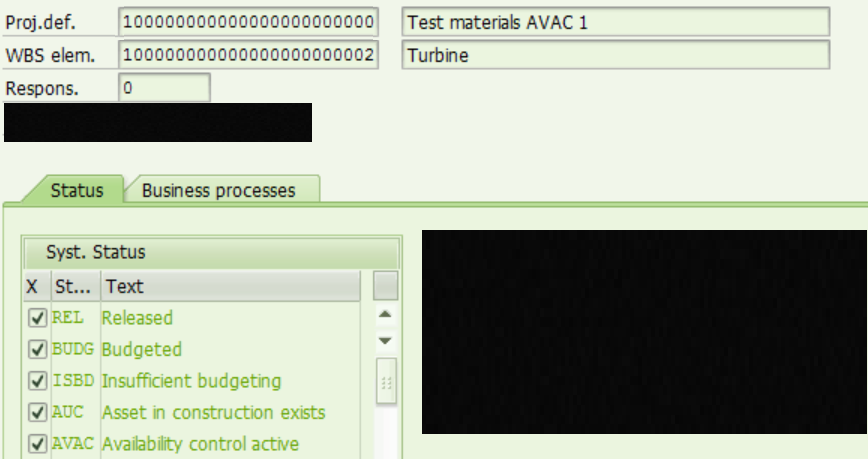
Availability control works exactly as expected. -100% overhead and material component planned costs are not taken into account. 100% overhead is interpreted as assigned value.
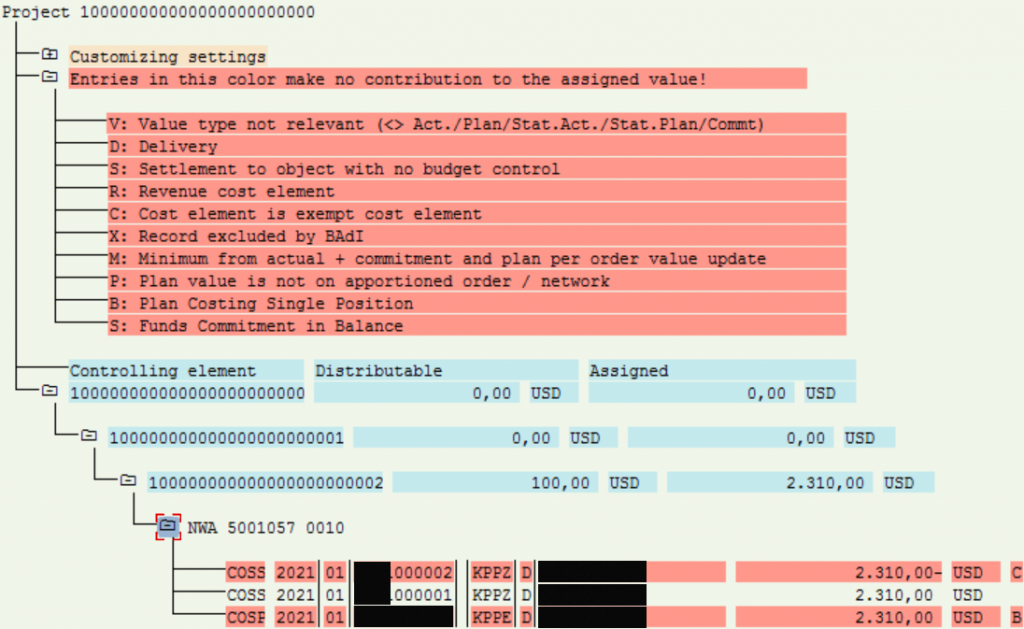
Reporting also works as expected and shows correct values.
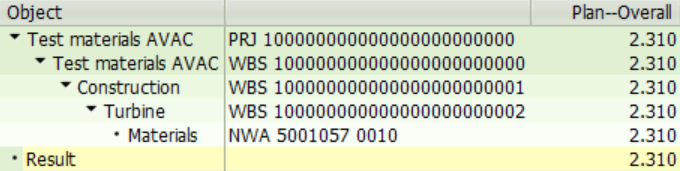