1. Introduction
Objective: to create a Configurable General Task List and Configured Equipment that will work in planned and corrective maintenance orders.
The basic process is shown below:
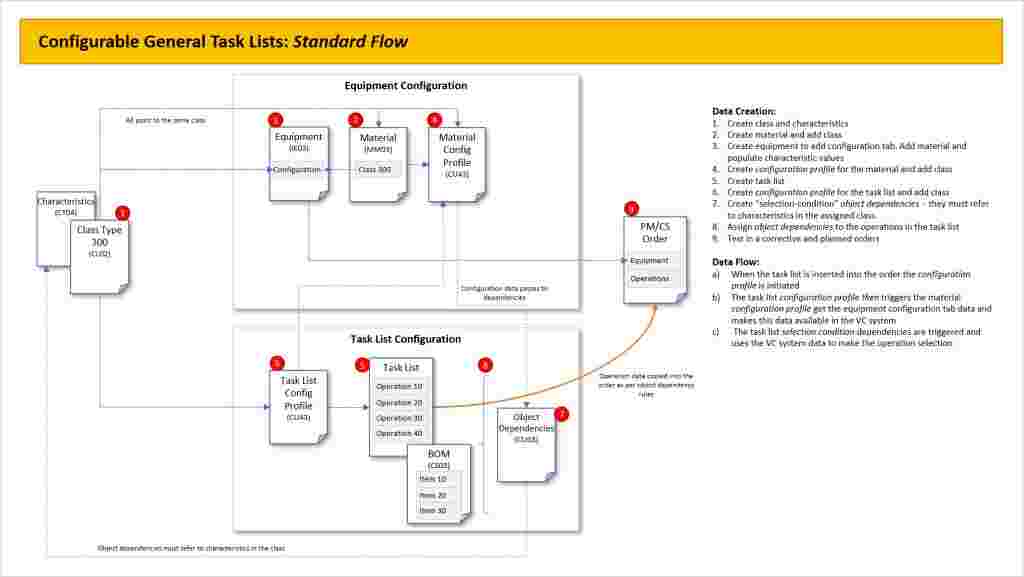
In this example we will create a task list with selectable operations based on whether the casing of a pump is cast iron, aluminium, or steel.
2. Configurable Materials
2.1 Define Class/Characteristic Data (CL02/CT04):
Create class type 300 and assign the characteristics as required.
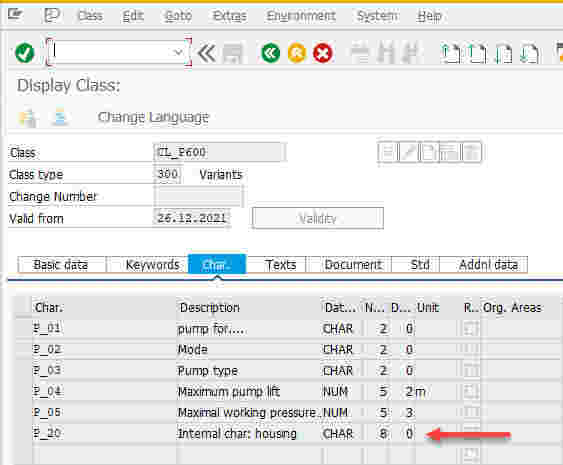
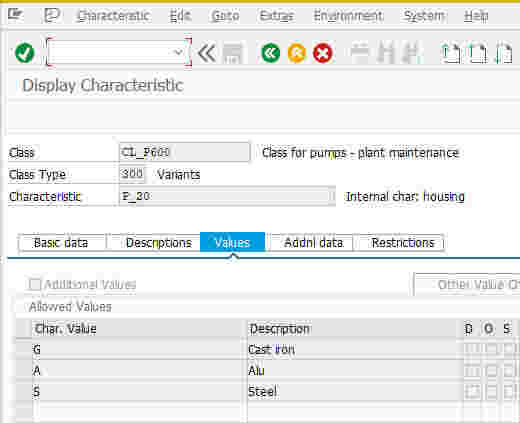
We will use characteristic P_20 later in our task list and equipment.
2.2 Create Configurable Material (MM01):
Create a new material and activate the Basic Data 1, Basic Data 2 and Classification tabs as a minimum.
Assign the class you created in section 2.1 above (you do not need to valuate the characteristics at this point).
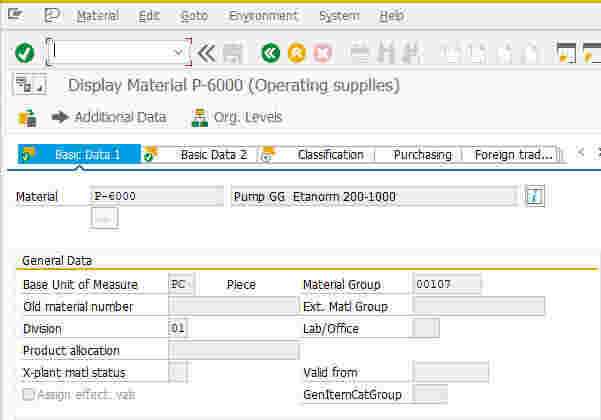
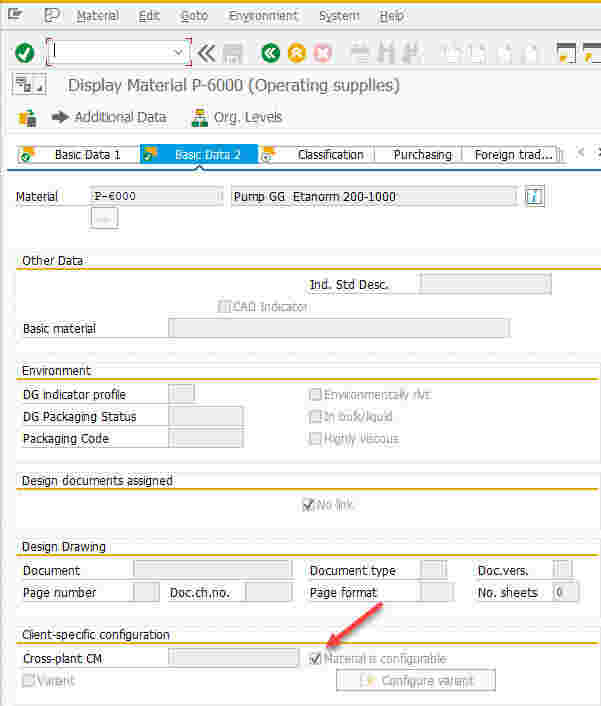
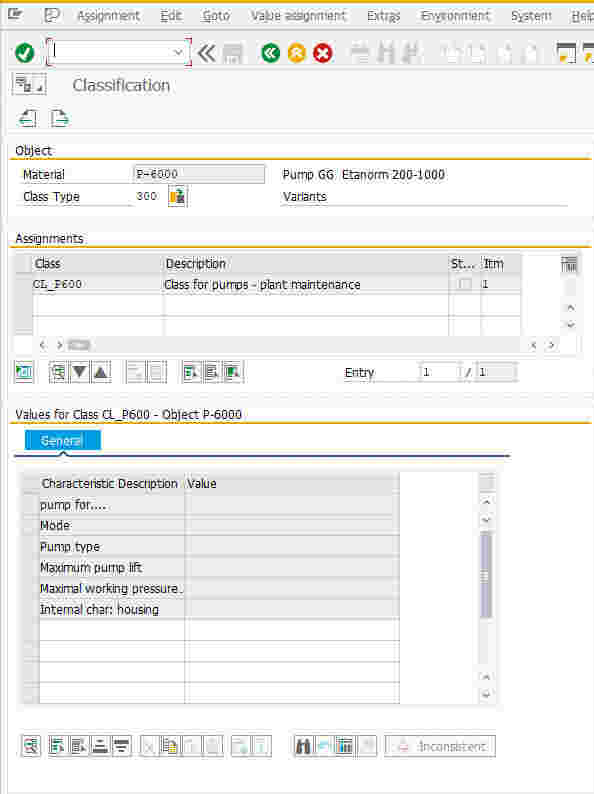
2.3 Create Configuration Profile for Material (CU41):
Create a configuration profile via CU41 for the material you created in section 2.2 above and assign the class.
Also ensure that the configuration profile is released.
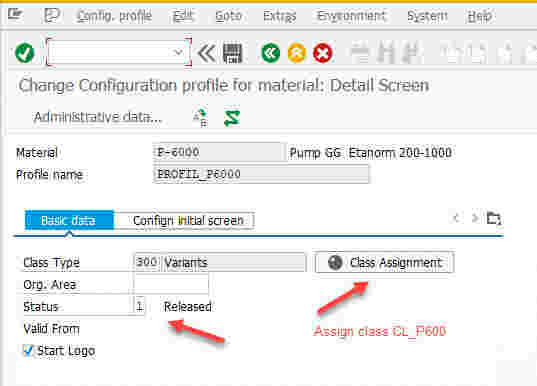
2.4 Assign Configurable Material to Equipment (IE02):
Go into the equipment master and activate the Configuration tab via menu path: Extras->View Selection, then select the Configuration checkbox.
On the Configuration tab, assign the configurable material you created in section 2.2 above. Then use the Maintain button to populate the characteristic values.
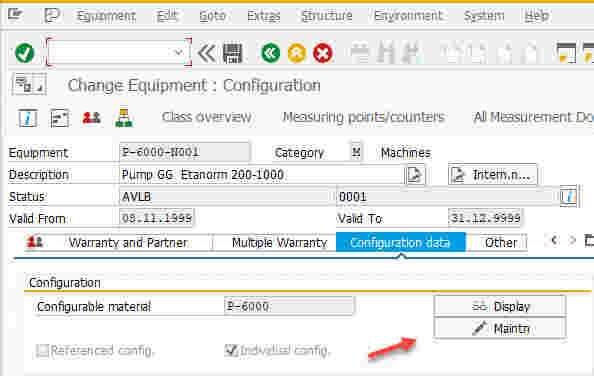
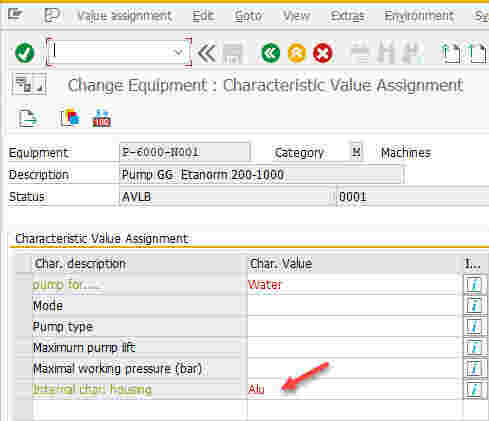
Make sure you populate the housing type as this will be used later in the task list.
Save the equipment.
3. Configurable General Task Lists
3.1 Create Object Dependencies (CU01):
Create new object dependencies (selection conditions) for each of the dependent operations you need to select.
Examples:
• Diesel engine
• Electric engine
The VC code format is =
Example: ENGINE_TYPE = ‘DIESEL’
Logical OR, AND, etc. functions can be used.
Example: ENGINE_TYPE = ‘DIESEL’ OR ENGINE_TYPE = ‘ELECTRIC’
In our case we are interested in characteristic P_20 and value “A”.
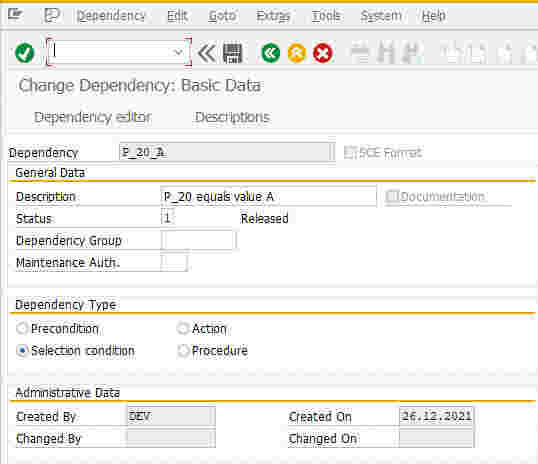
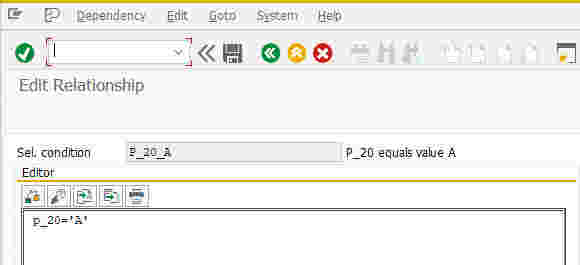
Create two more object dependencies for values “S” and “G”.
Ensure the dependencies are released.
3.2 Create General Task List (IA05):
Create a general task list and assign the relevant operations.
Then use menu path: Extras->Object Dependencies->Assignments to assign the object dependencies you created in section 3.1 above.
Note: do not assign dependencies to those operation which you want to always transfer to the order.
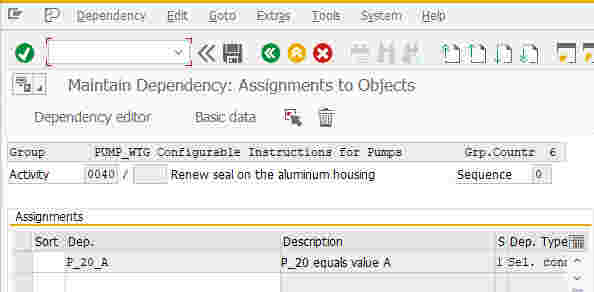
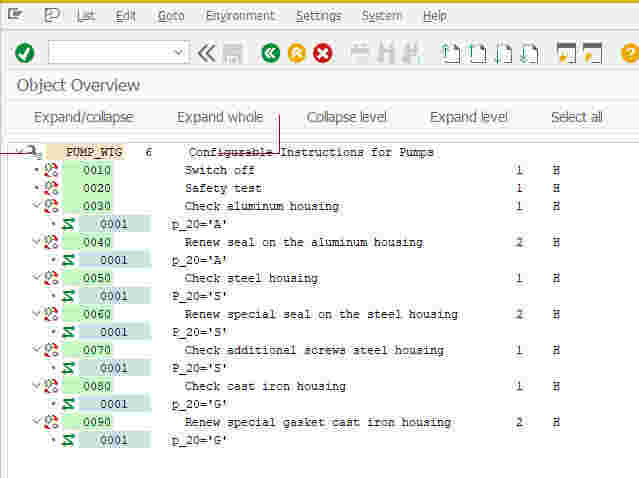
3.3 Create Configuration Profile for General Task List (CU41):
Create a configuration profile for the general task list you created in section 3.2 above and assign the class defined in section 2.1 above.
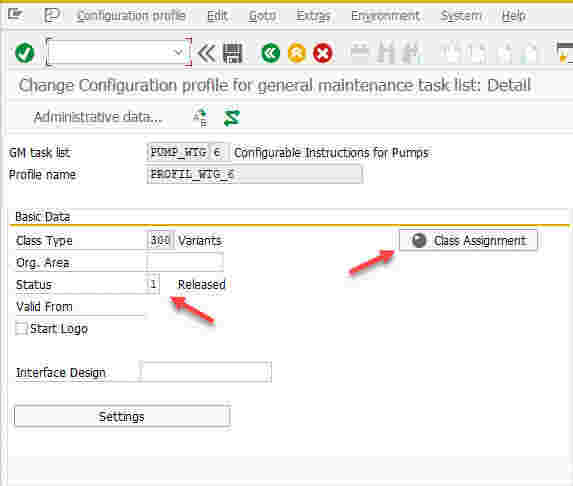
Ensure the profile is released.
4. Testing
4.1 Testing with Manually Assigned Task Lists (IW31/2):
Create or change an existing order and ensure that the configured equipment is entered in the order header.
Select the configurable general task list via menu path: Extras->Task List Selection->General Task List:
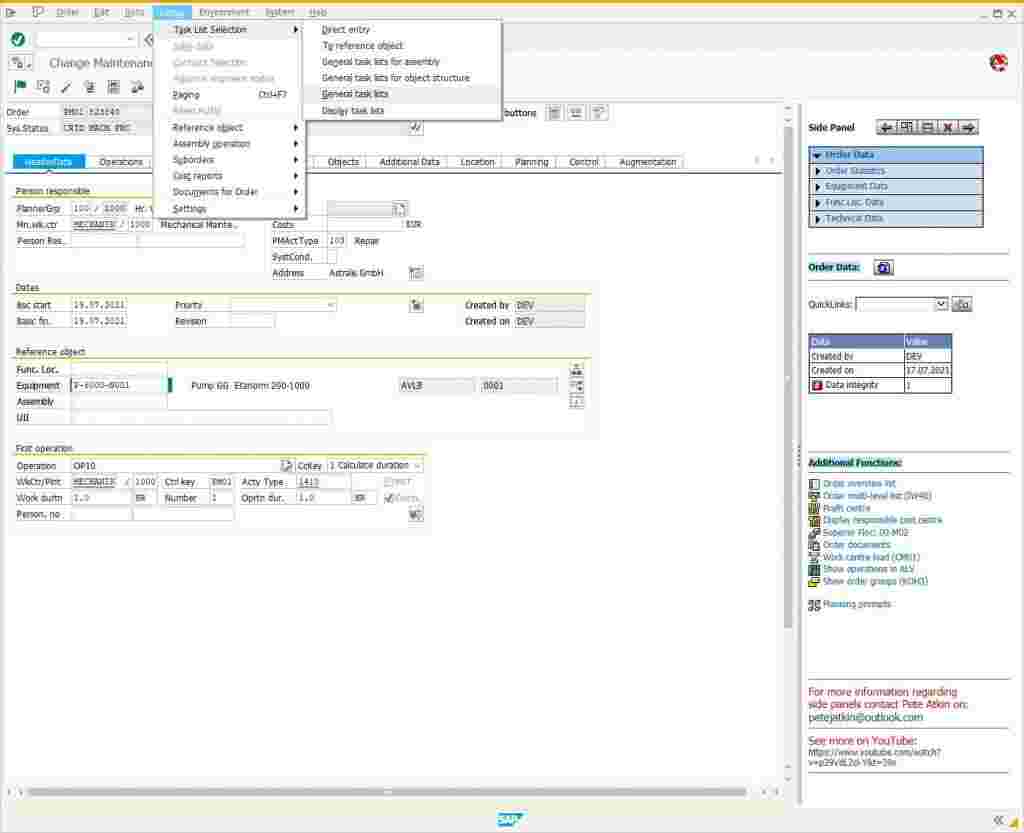
A classification screen should now be displayed and the characteristic values copied from the equipment. You can change these if required. Notice that the values have been derived from the equipment master:
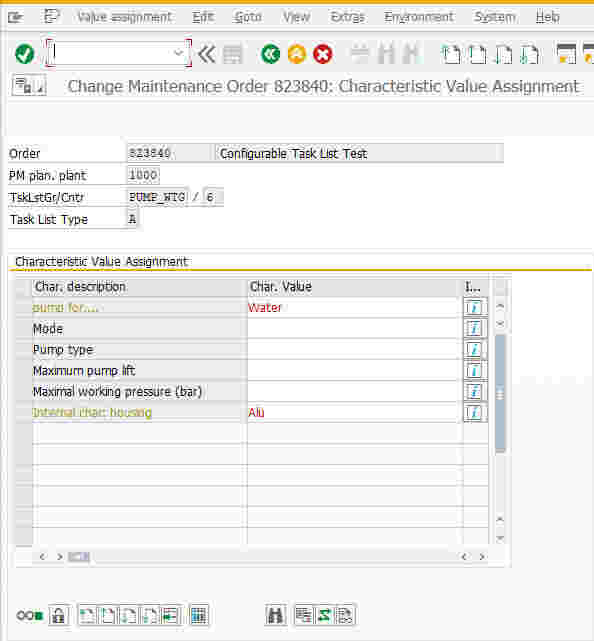
Green-arrow back out of this screen and the order should now be updated with the relevant operations i.e. those operations that satisfy the object dependency parameters, or those operations with no object dependency assignments.
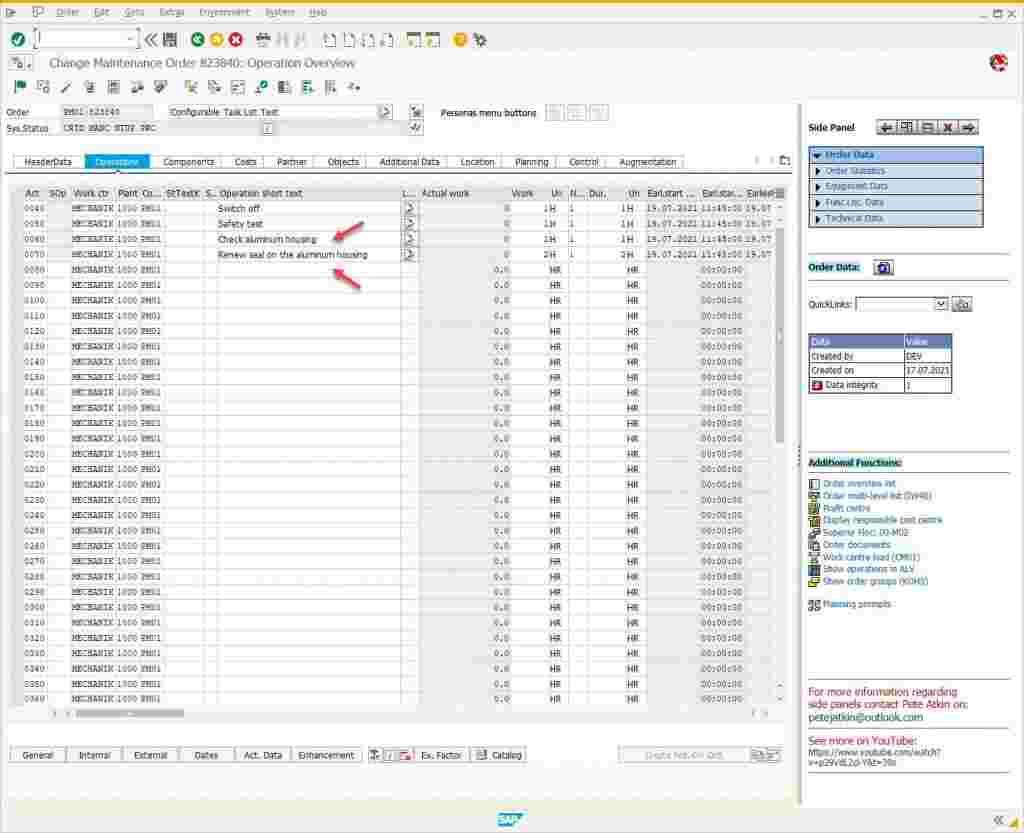
4.2 Testing with Maintenance Plans (IP10):
Create a maintenance plan for the configurable equipment you created in section 2.4 above.
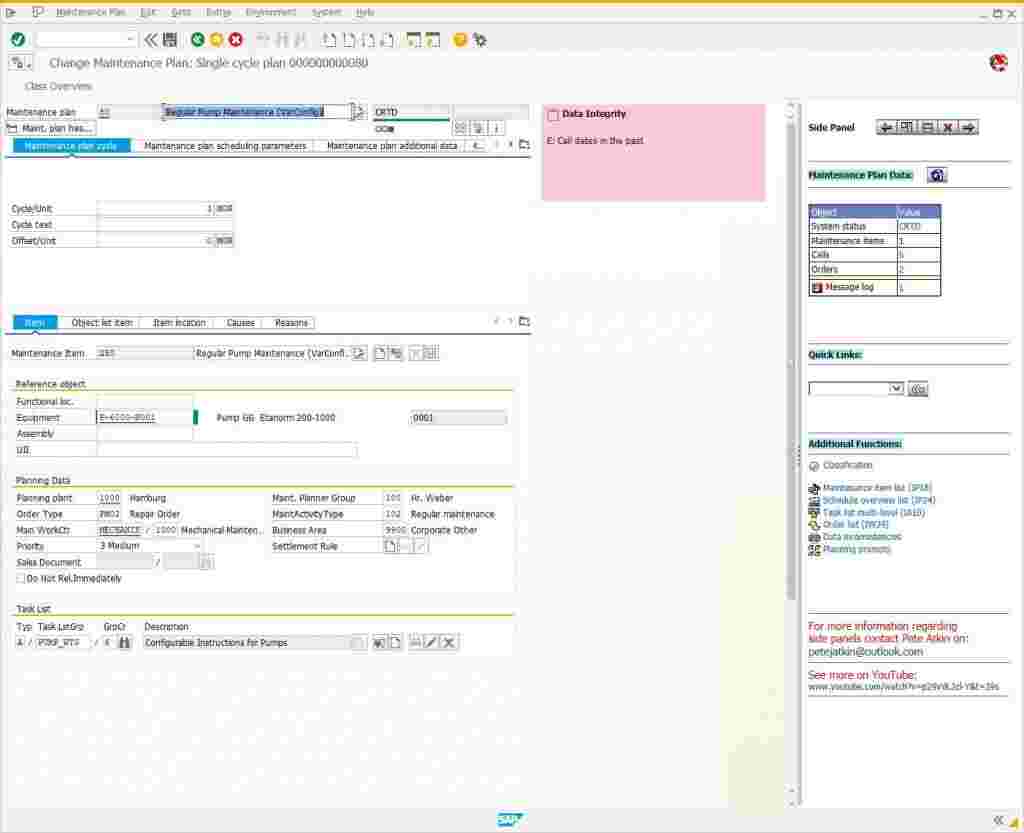
Schedule the plan via IP10 and release one of the calls.
The order should now be created with the relevant operations i.e. those operations that satisfy the object dependency parameters, or those operations with no object dependency assignments. Notice that the classification popup does not appear in this case.
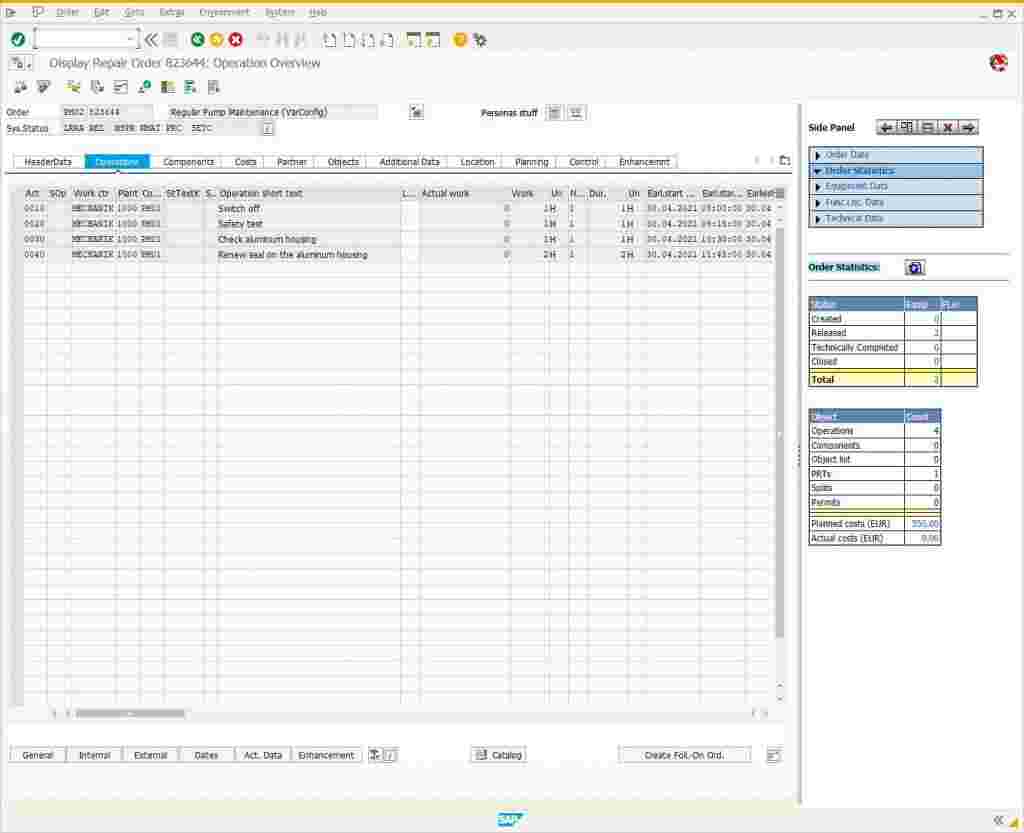