I wanted to share a key enhancement (Demand Management) to the SAP IBP Order Based Planning OBP capability to support the sales order confirmation process. Read content below to understand the business requirement, SAP IBP functionality gap, solution approach, and business value, when it comes to sales order confirmations using IBP Order Based Planning.
Introduction:
- This enhancement is built on top of the standard SAP IBP Response and Supply application, S/4 add-on for IBP, and S/4HANA Sales Order Processing capability.
- As you may know, SAP S/4HANA is tightly integrated with IBP Response and Supply for bi-directional data transfer (using S/4 Add-on for IBP and Smart Data Integration SDI). This helps sales orders to be planned and confirmed from SAP IBP into S/4HANA.
- However, the tight integration is a double-edged sword. It accelerates value delivery due to the out of box data integration, but it limits the options for planners to influence the planning process and apply their judgment in terms of planning in IBP with alternative requested dates or publishing alternative confirmed dates back to S/4HANA.
- With this Demand Management enhancement developed by GitaCloud team, planners can get the best of both worlds: tight integration offered by SAP IBP standard software as well as a loose coupling that enables the planning business process to have a manual validation and date edit capability both ways.
- See overall IBP Solution Architecture view below before we dee-dive into Demand Management processes.
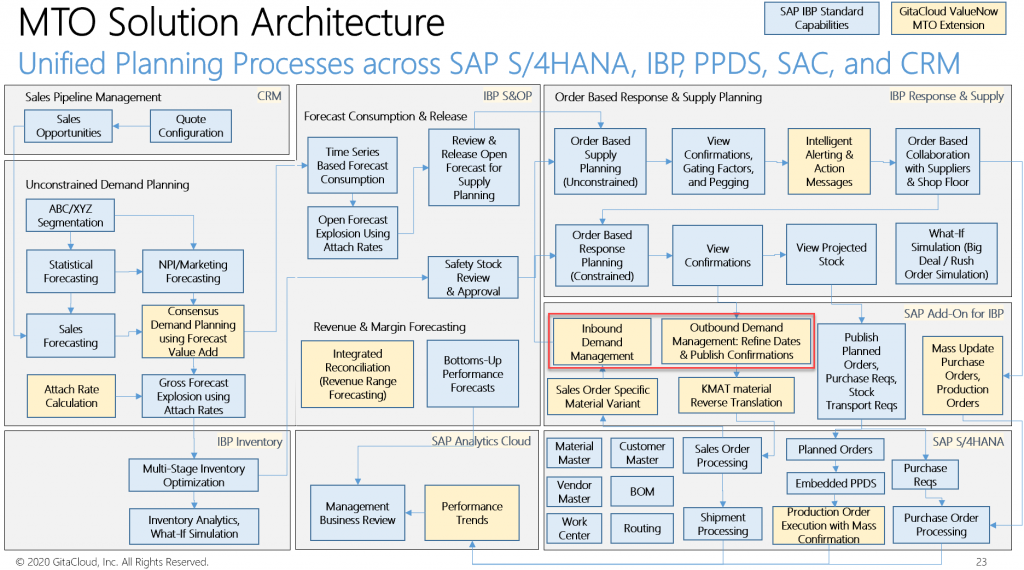
Business Requirement:
- Response Planners in the High-Tech industry and/or in the Make-To-Order industries have a double whammy of a volatile sales order backlog coupled with complex configurable build, which is constrained by both capacity and critical materials with long lead times.
- Customers often drop sales orders within the cumulative lead time required to procure and manufacture from scratch. Customers can continue to refine their desired configuration and requested dates even after placing a ‘firm’ order on the High-Tech or complex equipment manufacturer.
- Planners have to walk the tightrope of accepting requested dates in order to win the order, and at the same time, are held to a high standard of 95%+ On-Time Delivery.
- Given these complex business environment (volatile firm demands, unstable firm supply), Response Planners provide delivery lead time guidelines to the Order Entry teams per configurable product or product family. For example: 4 weeks from current date for Family 1; 8 weeks from current dates for Family 2, etc. Order Entry is expected to adhere to these guidelines when placing orders, but may violate them, if the Sales team deems the demand to be a flight risk with current delivery guidelines.
- However, given a specific configuration and accessories ordered by the customer, the current stock / capacity situation, and deliberate violation of delivery lead time guidelines, this can lead to undesirable ripple effect on confirmed backlog.
- Planners need to be able to plan sales orders with alternative requested dates (less or more aggressive than the date entered on S/4 Sales Order by Order Entry per current delivery lead time guidelines).
- Planners also need to be able to confirm sales orders in S/4HANA with alternative confirmed dates (less or more aggressive than the date generated by IBP OBP).
SAP IBP Capability Gap:
- SAP IBP plans on a Just-In-Time JIT basis (to minimize excess inventory investment) and does not incorporate a time buffer to mitigate risk to ensure on-time delivery in the face of unstable supply.
- SAP IBP runs based on a deterministic planning approach (not a stochastic planning approach): it computes order confirmation dates based on lead times and capacity data that does not factor the uncertainty range and hence the confirmation risk).
- The planner does have the option of simulating sales order demands for confirmation dates with alternative statement of capacity, lead times, etc., but the confirmed dates generated in the base version are not directly editable to reflect planner’s judgment of risk buffer required.
- Planners need an intuitive front-end where they can see both the S/4 requested date and IBP generated confirmed date(s) and be able to edit both and essentially ‘disconnect’ the sales order dates across S/4 and IBP.
- For example, Planner may want to drive IBP with a more aggressive requested date than in S/4 to buy a time buffer in case supply plans go awry.
- Planner may also want to do both: drive IBP against a more aggressive request date (to generate planned orders / purchase requisitions with a time buffer) and still put an additional buffer in terms of confirming the sales order in S/4 with a confirmed date later than the IBP proposed confirmed date.
- Planners need to be able to evaluate the S/4 sales order commercial risks as well: delivery blocks, complete delivery indicators, Order Entry comments, etc. in a single user-friendly screen, and not have to simultaneously open both S/4 and IBP applications with fragmented views of relevant data.
- Complete Delivery flag on S/4 Sales Orders is at a header level and not understood by SAP IBP, as it plans demands independently at sales order item level.
- Planners need an easy way to mark sales orders as not planning relevant based on delivery blocks / credit blocks. This is not feasible given the tight data integration across S/4 Sales Orders data and IBP OBP Data Model (Order Based Planning Area).
- SAP IBP has recently enabled interactive planning on planned supply elements (planned orders, purchase requisitions, etc.).
- Currently, SAP IBP does not currently allow date changes on firm demand elements.
- Planners essentially need a user-friendly Demand Management capability to manage sales order backlog on top of the tight integration offered by SDI. See solution details below to understand how these gaps have been addressed.
GitaCloud Solution Enhancement: Demand Management
- See Solution Architecture view below to understand how Demand Management Fiori App sits in between S/4HANA and IBP processes.
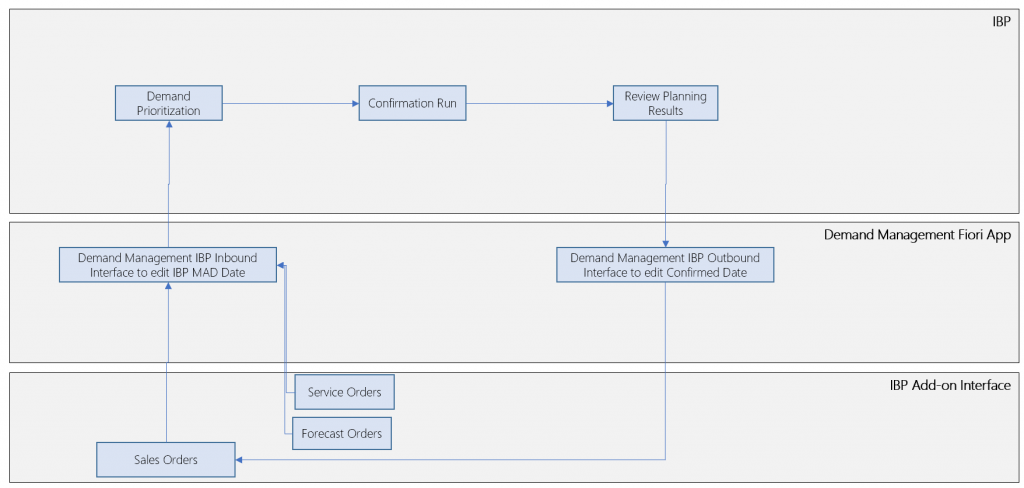
- See process flow below to understand how Demand Management augments the standard S/4-IBP integration and IBP Order Based Planning processes.
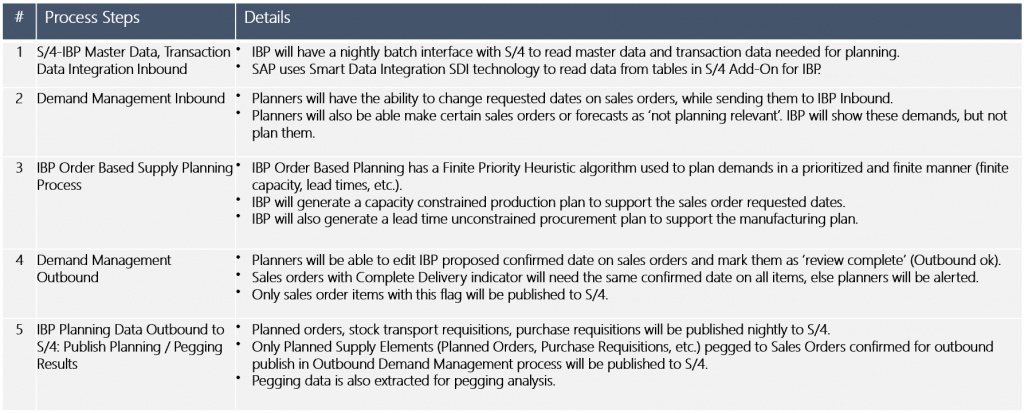
- See examples below to understand the inbound and outbound demand management processes.
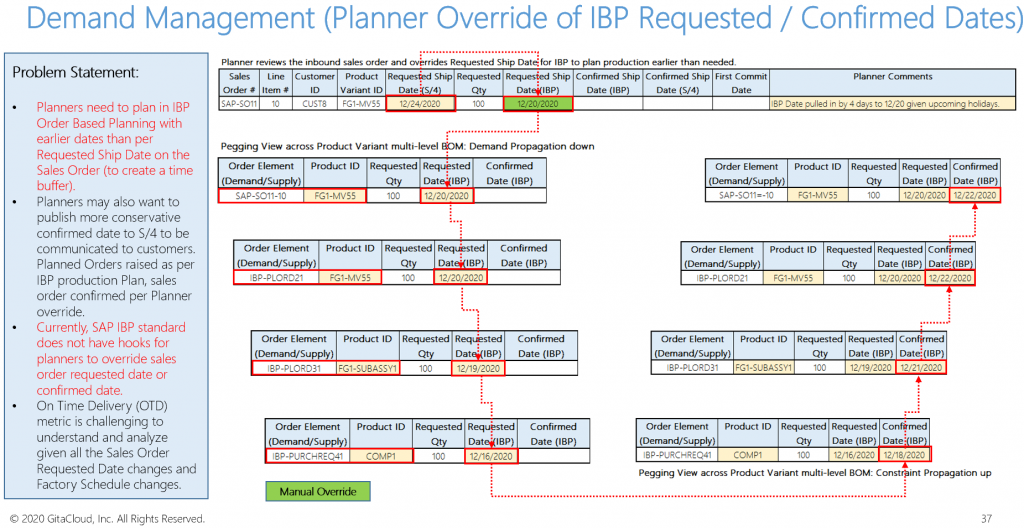
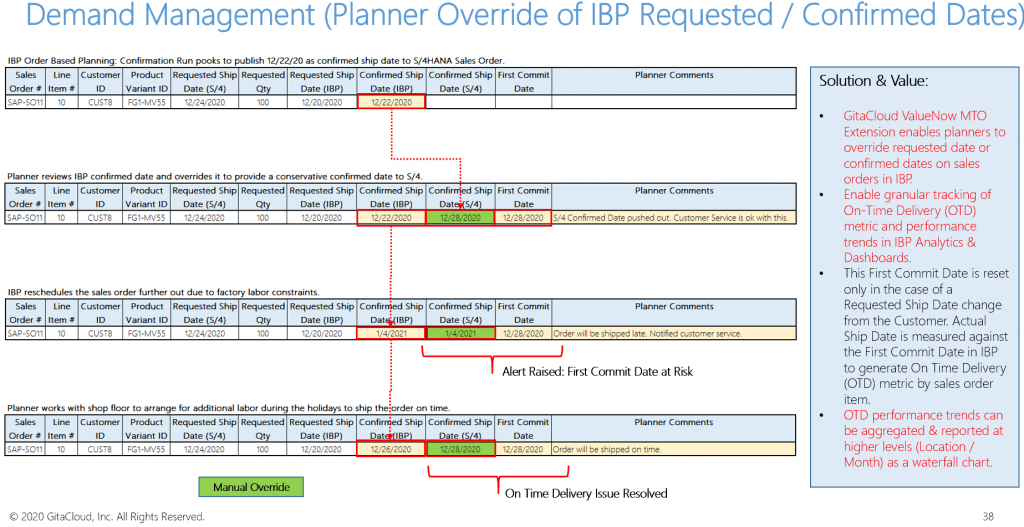
- GitaCloud team has developed a user-friendly Fiori App called Demand Management in the process interface between S/4HANA Sales Order Processing and IBP Order Based Planning.
- This app enables the planners to pull up sales order items based on flexible selection criteria: Planner Code (MRP Controller), Customer # or Name, Product # or Description, Location # or Name, Sales Order # / Item #, Requested Date Range, Confirmed Date Range, Sales Order Confirmation Status, etc.
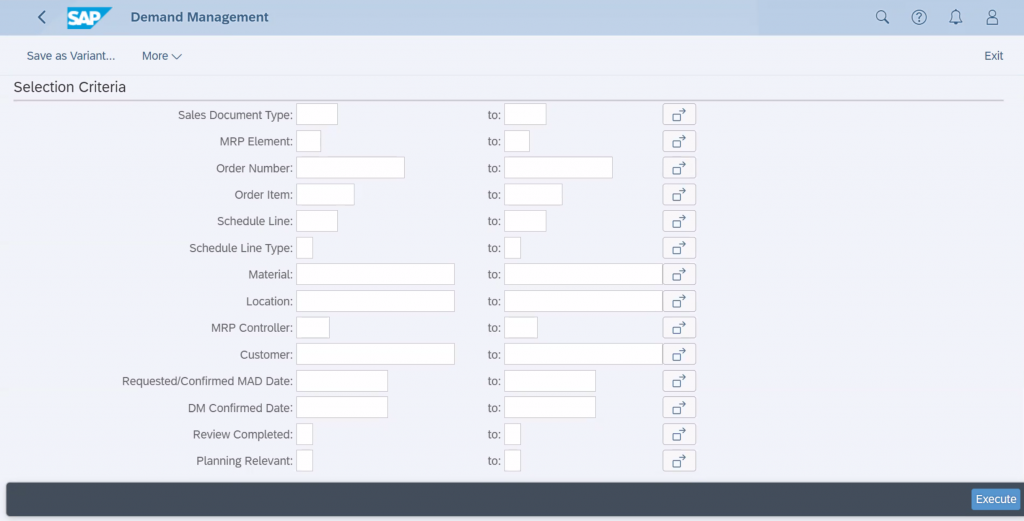
- Inbound Demand Management: Planners can pull up relevant order items and choose to review Sales Order Item Requested Date and validate that these dates meet the Product Family specific Delivery Lead Time guidelines.
- Planners can choose to set a flag manually “Inbound ok”, once they are done with the inbound review.
- SDI interface can be enhanced to only send sales order items to SAP IBP OBP when this flag is set. This ensures that the Planner review has occurred before the new Firm Demand is sent to IBP for Planning.
- Planners can freely define rules by product family, sales order type, etc. to also let a sub-set of demand to flow in automatically into IBP with S/4 requested dates.
- This app is available real-time to Planners, i.e., a sales order saved in S/4 is immediately visible for planner review in this app.
- Outbound Demand Management: Planners can choose to review Sales Order Items for IBP proposed confirmed dates and provide a different date in the S/4 Confirmed Date field.
- Planner needs to set a flag “Outbound ok” after they complete the confirmation review / date edit.
- Only the Sales Order Items confirmed by Planners are published to S/4. Also, only the proposed supply elements (planned orders / purchase requisitions) pegged to the confirmed sales order items are published to S/4.
- See snapshots below to understand a sample list of the sales order fields available to Planners.


Business Value:
- Current IBP to S/4 outbound publish interface for planned supply is not related to the sales order confirmation status. This means proposed supply elements could get published to S/4 even when the Planner has not reviewed the Sales Order Item confirmation date(s).
- Imagine a scenario in which Order Entry enters 10 orders for a given material. 2 of these orders have unreasonable requested dates, which drive incorrect demand prioritization, and corresponding proposed supply elements which are not needed as early as planned by IBP. Planners need to control when it is ok to publish such proposed supply elements in order to mitigate execution risks in stressing the supply base (production plants, suppliers, etc.) needlessly.
- Planners need a friendly way to review new firm demands both inbound and outbound and ensure IBP is reflecting their priorities as well as S/4 sales order confirmations reflect a time buffer based on planner experience to mitigate risk to customer satisfaction.
- Planners also get a user-friendly interface to turn off planning relevance altogether for sales orders not yet solidified from order configuration perspective or having credit issues, etc.
- Planners also get to see which sales order items need to be shipped together due to a Complete Delivery indicator on the Sales Order Header level. Demand Management App provides a warning to the Planner in case sales order items for a complete delivery order do not all have the same confirmed date.
- Planner can now decide whether they want to change the dates manually or make IBP plan these items against an alternative request date.
Rating: 0 / 5 (0 votes)