Scenario:
Creating the Advanced Return order which generates the Customer RMA number automatically with specifying the details about refund or replacement of material required.
Return delivery also created automatically and PGR need to be done for receiving the goods from customer then Quality Inspection team will do the inspection of the received material and release the free of charge replacement material to customer via automatically created SDF (Subsequent Delivery free of charge) document in SAP S/4 HANA 1809 system.
There are many other features in Advanced return management except replacement material like complete refund, partial refund, Inspection already done when placing return order, etc. which is also explained below.
Step 1:
Activate Advanced return management for return order type:
In Customizing for Sales and Distribution, choose > Sales > Advanced Returns Management > Activate Advanced return management for Return Order Types
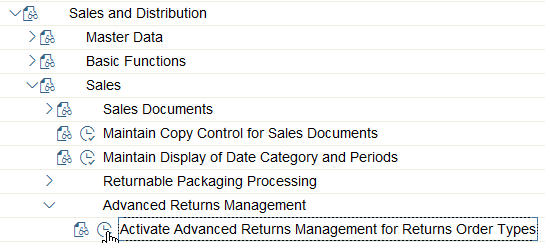

Step 2:
Scenario: Wrong material sent (or any other reason) to customer and customer want replacement of the material.
Create Advanced return Order:
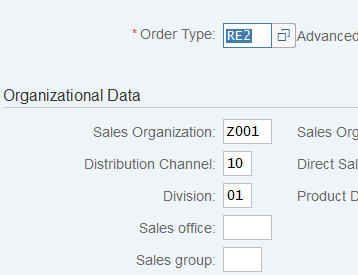
There is a specific tab “Returns” where all the details regarding advanced return need to be entered.
Refund Type: You can choose refund type accordingly that you want to give replacement material to customer or refund for the material.
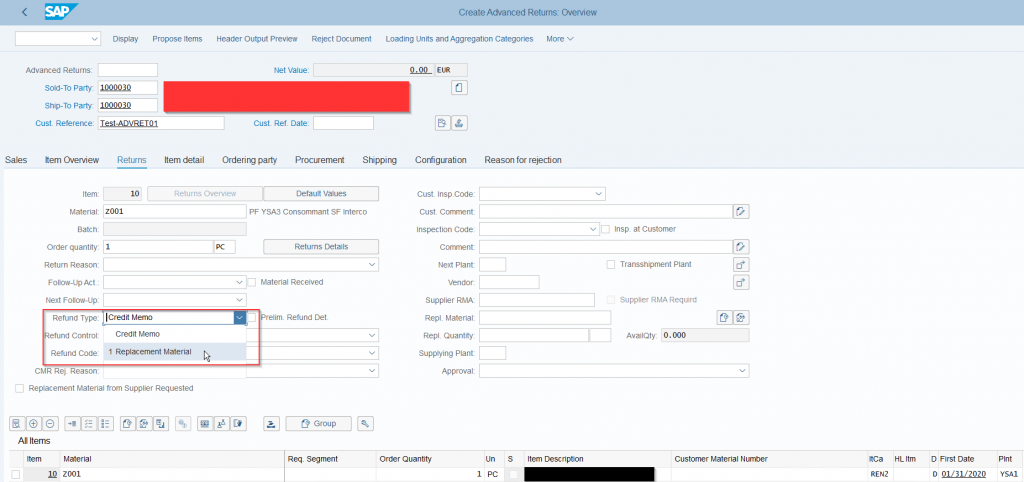
If you want to give refund then you can also choose how much refund need to be processed by Refund Code field:
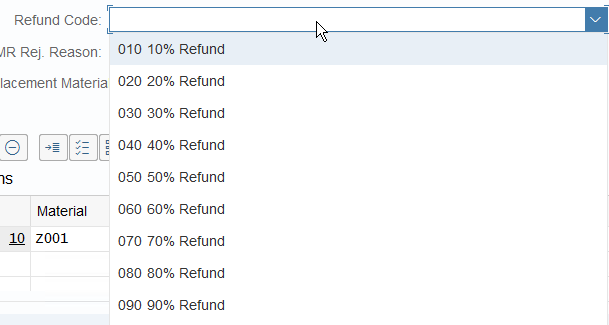
Step 3:
After choosing Refund Type – You have to select Refund Control to specify when replacement material (or credit memo) will be sent to customer.

You can mention the Replacement material which you want to send with its quantity and supplying plant.
Available quantity will be shown in the same screen as per the material entered as replacement material and supplying plant.
Refund Type:
- Choose I Immediately or P Approved if you want to create a subsequent delivery free of charge (SDF) right away. This process depends on whether or not you have already received the material. If you choose I Immediately, the system also creates the delivery for the SDF and posts the respective goods issue.
- Choose R By Credit Memo Request or A After Receipt of Credit Memo if you want to postpone the decision regarding a return to a later time. You can then release an SDF in the Material Inspection in Warehouse transaction and the Customer Return Determination transaction. The refunding type – Replacement Material that is specified in the returns order is displayed in both of these transactions so that the person making the next decision knows that the customer would like a replacement material. You can only use refund control A if you specify a logistical follow-up activity in which the material is sent to an external vendor or is transferred to a plant with a different company code.
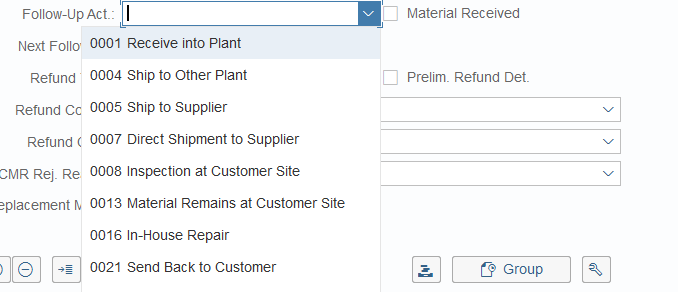
Follow – up Action need to be chosen to get the material from customer and send it to respective locations:
Follow-Up Activity Code | Default Description of Logistical Follow-Up Activity | Meaning |
0001 | Receive into Plant | Returned materials are posted to the returns warehouse (usually to blocked stock). |
0002 | Immediately Move to Free Available Stock | Returned materials are posted to unrestricted-use stock (usually with stock type Unrestricted-Use Stock). |
0003 | Immediately Move to Scrap | Returned materials are temporarily posted to returns stock and then a goods issue is posted to scrap. |
0004 | Ship to Other Plant | Returned materials are sent to another plant. The materials are posted to returns stock first. |
0005 | Ship to Vendor | Returned materials are sent to an external vendor. The materials are posted to returns stock first. |
0006 | Ship to Vendor Via Other Plant | Returned materials are sent to an external vendor via another plant. The materials are posted to returns stock first. |
0007 | Direct Shipment to Vendor | The customer sends the return material directly to an external vendor without returning it to your company. |
0008 | Inspection at Customer Site | You choose this activity if you want to inspect the material at the customer site before it is returned. Once you have the inspection results, you decide whether the material should be sent back or if it should remain with the customer. To do so, you change the logistical follow-up activity in the returns order. |
0009 | Delivery into Plant — Materials Still Unknown | Choose this activity if you cannot exactly specify the materials and quantities to be returned. A returns delivery is posted and when the goods are physically received, you can update the returns order with the returned materials. |
0013 | Material Remains at Customer Site | Choose this activity if you decide after the inspection at the customer site that the material should stay with the customer. It might be scrapped there, for example. The customer can be refunded in the usual way. |
0014 | Immediately Move to Specified Stock | The returned material is posted to a specific kind of stock (such as stock for second-grade goods). |
0016 | In-House Repair | An in-house repair is triggered for the returned material using a corresponding repair order. You can configure an automatic goods movement from the returns stock to the repair order stock. |
0017 | External Repair | An external repair is triggered for the returned material using a corresponding repair order. You can configure an automatic goods movement from the returns stock to the repair order stock. |
0021 | Send Back to Customer | Returned materials are sent back to the customer. |
You can deactivate any unnecessary logistical follow-up activities in Customizing for Advanced Returns Management by choose > Sales > Advanced Returns Management > Activate and Rename Follow-Up Activities . You can also replace the default descriptions of the follow-up activity codes with your own descriptions.
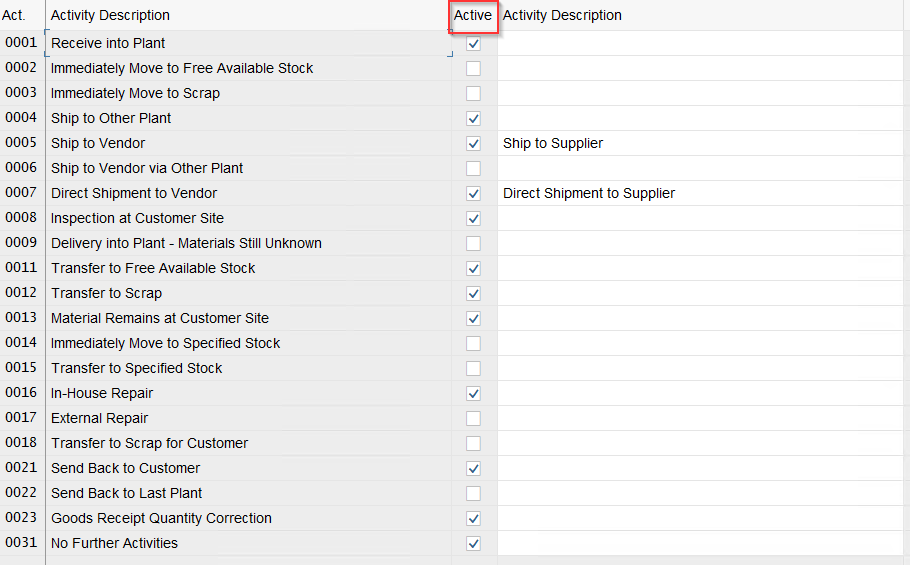
Material Inspection:
If you have already received the returned material when you enter the returns order (because it was returned at the counter, for example), you can enter the inspection results directly in the returns order.
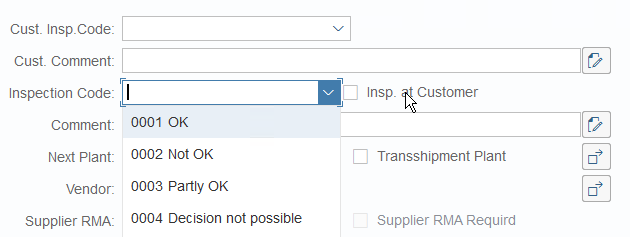
You have not chosen this option in our current scenario and Quality inspection team will do the inspection after receiving the product from customer.
Save the return order after below entries in Return tab.
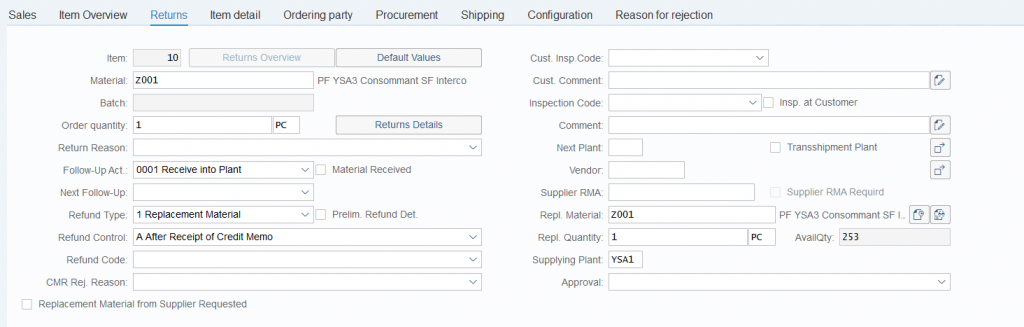
Step 4:
Check the return Order and Customer RMA number created automatically which is used between Customer and Client as unique number which will flow in all the documents for tracking purpose.
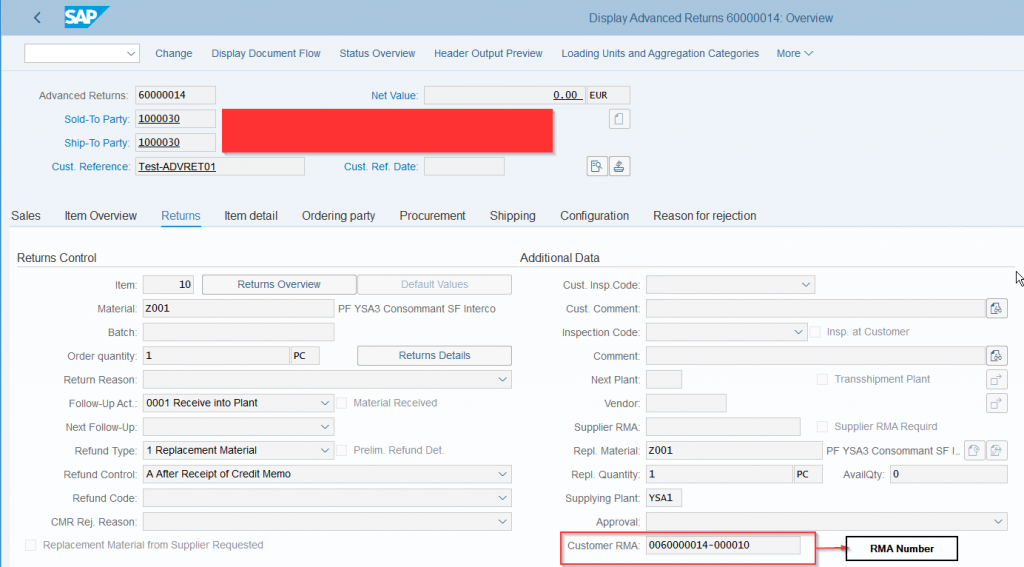
Advanced return delivery is also created automatically:

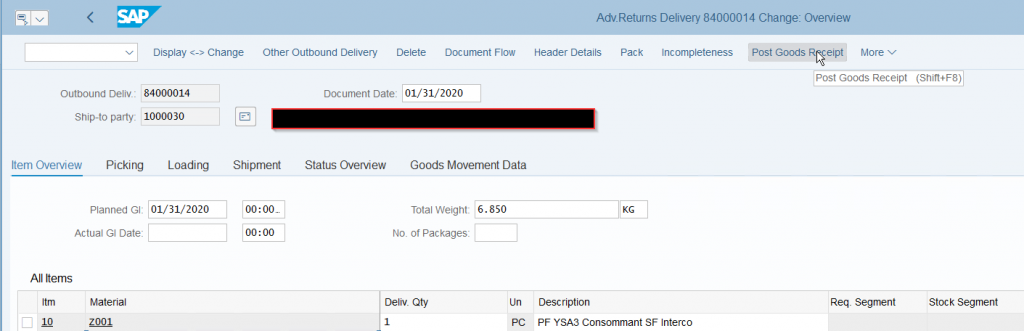
PGR need to be done for receiving the goods in our premises.
Step 5:
You can check the complete flow of Advance return management from Returns Overview button present in Return tab of Return order.
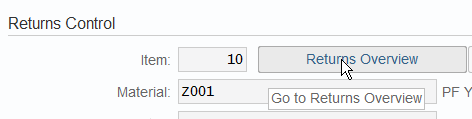
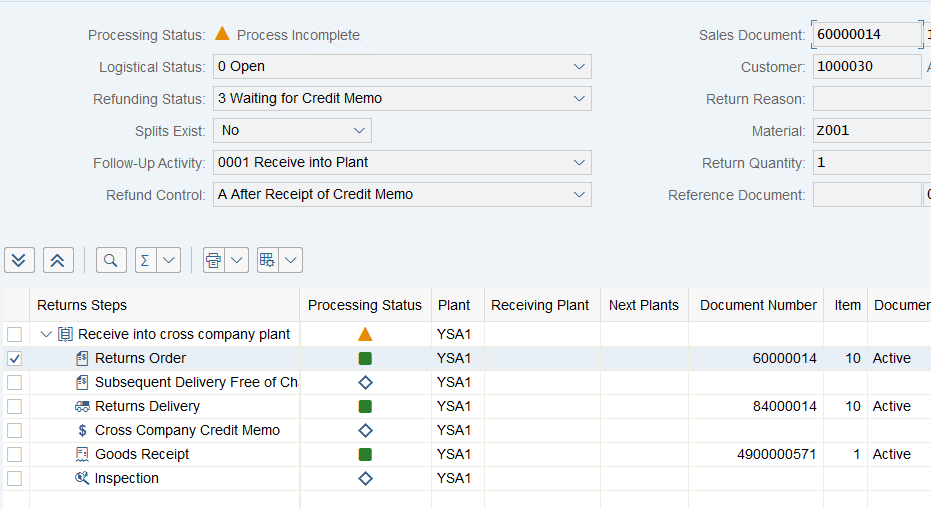
NOTE: I have used cross company plant that’s why Cross company credit memo and other details are shown in picture, You can ignore that part.
Step 6:
After Goods Receipt, Inspection need to be done and if item is okay then Quality inspection team need to release the Subsequent delivery free of charge (SDF) for the customer to send replaced material.
Run the transaction: MSR_INSPWH and enter the customer RMA number in the selection screen (or other details can be entered).
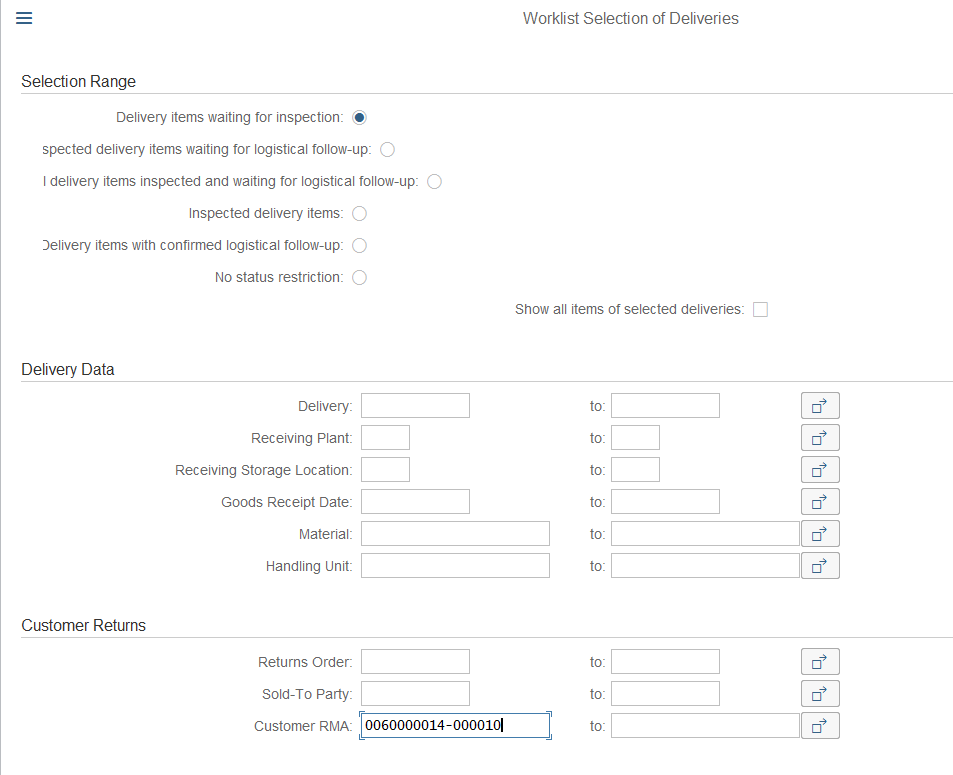
Header >
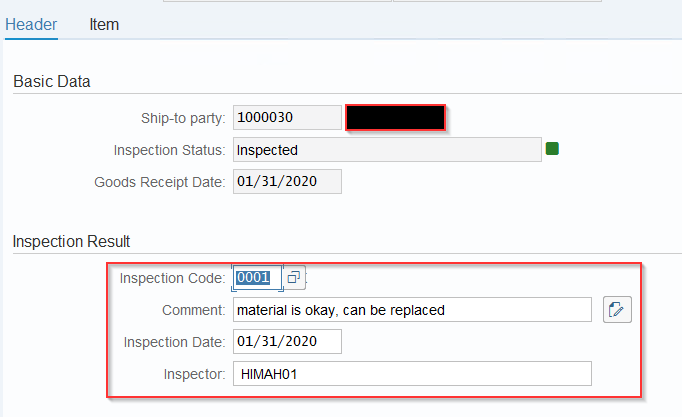
Item >
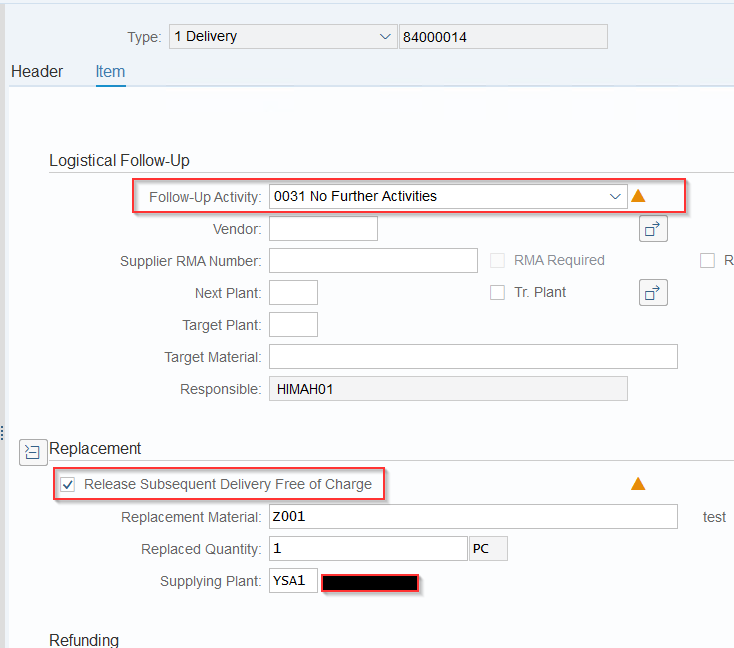
- Release the SDF document.
Material is okay, otherwise in Follow-up activity – you can choose options like In-house repair needed, etc. (If this activity is activated which is explained above).
- Click on Save & confirm button.
Current Status in Return order:
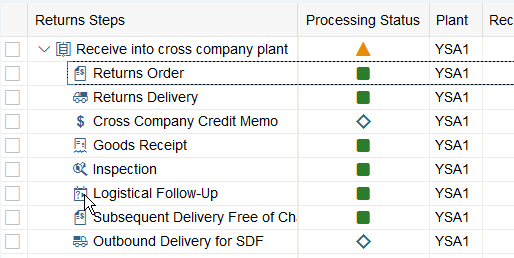
Step 7:
Create delivery & PGI for Subsequent delivery FOC document:
Same RMA number also copied to SDF:
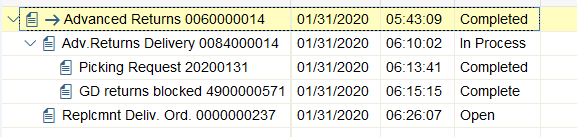
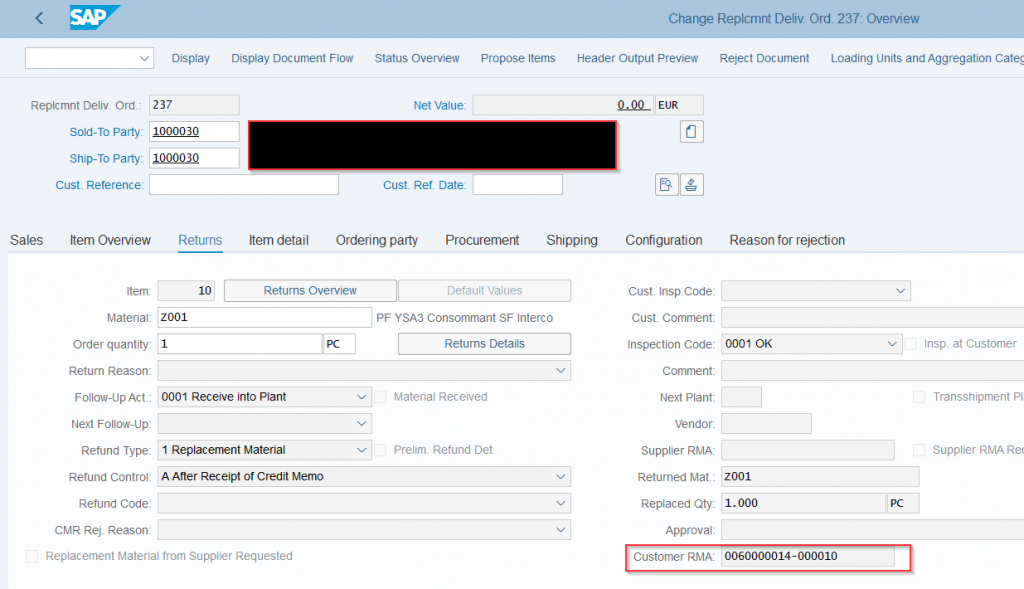
100% discount applied to SDF:
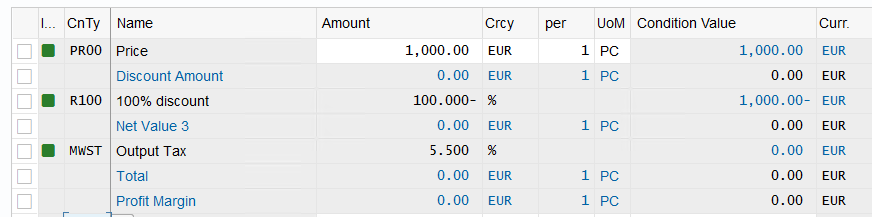
Create delivery and PGI.
Return Overview of return order:
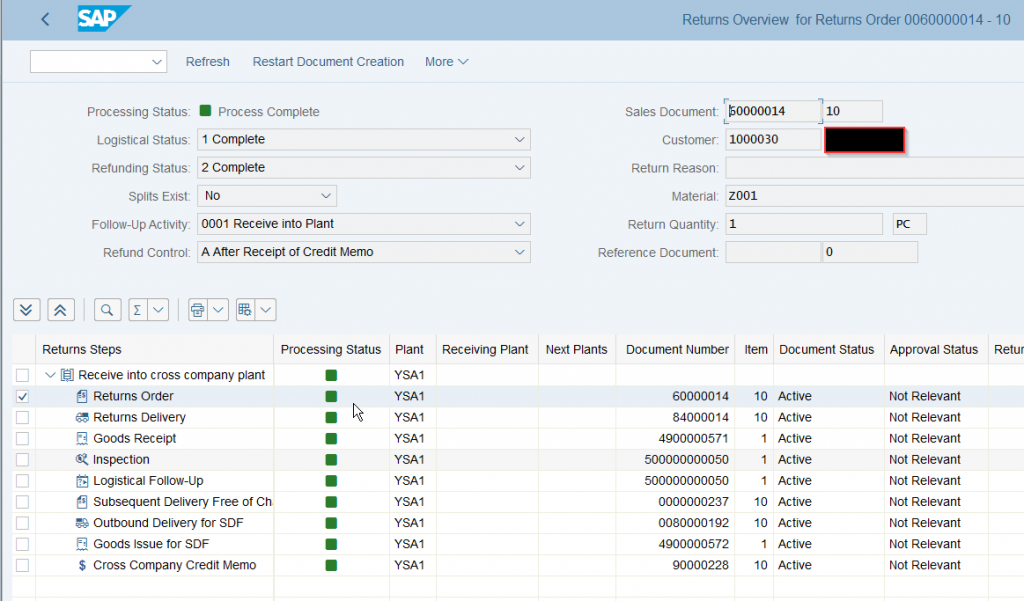
All processing statuses are now completed and all the lights are green.